Keine Zukunft ohne integrierte Produktions- und Logistiknetzwerke
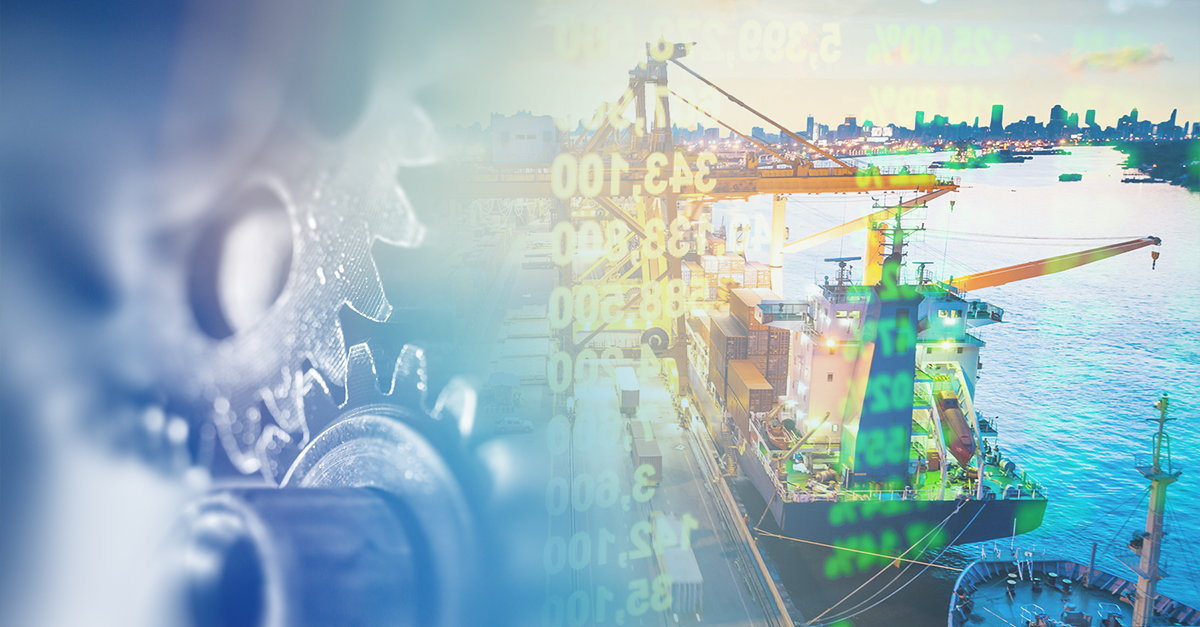
Über flexible Produktions- und Logistiknetzwerke ist gerade in wirtschaftlich turbulenten Zeiten schon viel geschrieben worden. Die Realität in vielen Unternehmen ist aber noch immer so, dass Produktionsprogrammplanung und die Logistikplanung unintegriert nebeneinander herlaufen. Auch die Integration der Lieferanten ist meist nur unvollständig umgesetzt.
Integrierter Ansatz ist elementar für eine resiliente Supply Chain
Dabei gilt es als erwiesen, dass ein integrierter Ansatz und eine wechselseitige Optimierung von Logistik und Produktion die Grundlage liefern können, um Unsicherheiten und Störungen rechtzeitig zu berücksichtigen und abzufedern. Dazu benötigt es Daten, die Downstream aus der Planung über die Logistik zum Lieferanten kommen und Upstream vom Lieferanten zum Kunden. Konkret bedeutet dies z.B. die Bedarfsvorausschau im kurz-, mittel- und langfristigen Horizont an den Lieferanten und umgekehrt die Kapazitätsvorausschau des Lieferanten an den Kunden bereitzustellen.
Smart Factory: Viele „Anfänger“, wenige „Vorreiter“
Leider ist die Industrie davon noch weit entfernt. So gelten laut einer aktuellen Studie von Cap Gemini 72 Prozent der Automobilunternehmen als „Anfänger“ bei der Umsetzung der Smart Factory und nur 10 Prozent sind „Vorreiter“ und damit gerüstet, das ganze Potenzial intelligenter Fabriken zu nutzen (bei den OEMs zählen 18 Prozent zu den Vorreitern, bei den Zulieferern 8 Prozent).
Tatsächlicher Bedarf wird zu wenig berücksichtigt
Eine auf den tatsächlichen täglichen Bedarf ausgelegte Planung und Steuerung der Abholzeitpunkte, Dimensionierungen und Pufferkapazitäten im Netzwerk ist meist nicht vorhanden und nicht auf die aktuell tatsächlich benötigten Materialien, Teile und Komponenten ausgelegt. Die dann folgende routinemäßige Nachjustierung ist kompliziert, aufwändig und teuer. Sie findet auf dem Domain-Know-how der Programmplaner und Disponenten statt, die oft nicht die optimale Lösung finden können, weil Ihnen die notwendigen Daten fehlen. Zumeist sehen sie nur die Daten aus dem eigenen Werk. Unternehmensübergreifende Daten zu Beständen, Lieferzeiten, Second-Source-Lieferanten etc. sind nicht vorhanden. Die Lösung des aktuellen Problems um jeden Preis steht dabei stets im Vordergrund, um eine Produktionsunterbrechung zu verhindern.
Partnerschaftliche Zusammenarbeit zwischen Kunde und Lieferant als Schlüssel zum Erfolg
Dabei wissen wir aber seit Jahren, dass in Zukunft zuverlässige und integrierte Produktions- und Liefernetzwerke über die Wettbewerbsfähigkeit und den Bestand eines Unternehmens entscheiden werden. Um dies zu erreichen sind Anpassungen im Umgang miteinander notwendig. Nur die partnerschaftliche und vertrauensvolle Zusammenarbeit zwischen Kunde und Lieferanten garantiert den langfristigen Erfolg. Damit wird es möglich, dass der Kunde aktuell seinen tatsächlichen Bedarf meldet und der Lieferant nicht bestraft wird, wenn er abweichend zurückmeldet.
Right-Time statt Real-Time
Eine moderne Lösung muss die Konzeption, Auslegung und die fortlaufende Anpassung von Materialversorgung und Auftragseinplanung unterstützen. SupplyOn verfolgt mit seiner Production-to-Supply-Lösung exakt dieses Ziel und ersetzt den heute noch weitverbreiteten Real-Time-Ansatz durch einen Right-Time-Ansatz: Daten aus dem Liefernetz müssen nicht ständig topaktuell sein, sondern nur zum Zeitpunkt einer Neuplanung, dann aber möglichst korrekt. Die Transparenz hilft dann eine Optimierungslogik aufzubauen, die die gegenläufigen Ziele von Produktionsprogrammplanung und Logistikplanung optimal kombiniert.
Erhebliche Vorteile durch Einsatz von künstlicher Intelligenz
Aktuell arbeitet SupplyOn an einer kognitiven Erweiterung der Production-to-Supply-Lösung, die eine Bewertung von Störungen vornimmt und automatisiert Maßnahmen zur Beseitigung vorschlägt. Da das System nicht nur über das Domain-Wissen eines Mitarbeiters verfügt, sondern über ein firmenübergreifendes Wissen, lassen sich Störungen früher erkennen und Vorschläge für eine optimale Lösung schaffen. Ziele sind eine Reduzierung des manuellen Aufwandes gegenüber der heutigen Situation um zwei Drittel, Vermeidung von Problemsituationen und um 50 Prozent verringerte Kosten für Sonderfahrten und Ersatzlösungen.
Möglich wird dies durch die vertrauensvolle Zusammenarbeit von Lieferant und Kunde: Bereitstellung verlässlicher Plandaten durch den Kunden und Lieferung von Kapazitäts-, Produktions- und Qualitätsdaten durch den Lieferanten.