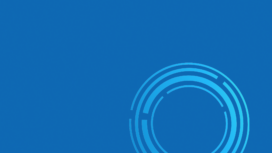
Überzeugte Kunden
Vendor Managed Inventory: Kosteneinsparung durch Transparenz bei der Franz Wolf GmbH
Die Konzentration auf Kernkompetenzen und ein optimaler Ressourceneinsatz sind heute eine Voraussetzung für den Markterfolg. Das gilt insbesondere für die Automobil- und Fertigungsindustrie, die mit einer hohen Prozesskomplexität und einer geringeren Fertigungstiefe konfrontiert ist. Kunden und Lieferanten suchen deshalb nach neuen Wegen, um ihre Beziehungen effizienter zu steuern. Vendor Managed Inventory (VMI), ein Ansatz bei dem der Lieferant die Verantwortung für das Management des Kundenlagers übernimmt, bietet dabei beiden Partnern Optimierungspotenziale. Die Firma Franz Wolf GmbH und Bosch setzen auf SupplyOn, um ihre Zusammenarbeit nach dem VMI-Prinzip zu organisieren.
Zu den wichtigsten Kunden des Unternehmens zählt die Robert Bosch GmbH, mit der Franz Wolf eine mehr als dreißigjährige Lieferantenbeziehung verbindet. Die Zusammenarbeit wurde in den letzten Jahren beständig ausgeweitet: Inzwischen liefert Franz Wolf Teile an Bosch-Werke in Deutschland, USA, Mexiko, Indien und China.„Die Rahmenbedingungen in unserer Branche haben sich in den letzten Jahren sehr verändert. Termin- und Preisdruck zwingen unsere Kunden und uns zu großer Flexibilität und beständiger Effizienzsteigerung“, sagt Petra Kaiser, die das von ihren Eltern gegründete Unternehmen heute führt. „Wir brauchen deshalb Kooperationsmodelle, die diesen Anforderungen gerecht werden.“ Als die Robert Bosch GmbH mit der Einführung von VMI auf Basis von SupplyOn begann, gehörte der Zulieferer deshalb zu den ersten Projektpartnern.
Vendor Managed Inventory mit SupplyOn
SupplyOn ermöglicht die Umsetzung innovativer Dispositionsmethoden, bei denen der Lieferant die Verwaltung des Lagers seines Kunden übernimmt. Dazu werden die Lagerbestandsdaten und Bedarfe angezeigt und für jeden Artikel maximale und minimale Lagerbestände vereinbart. Auf Basis dieser Daten disponiert der Lieferant das Lager seines Kunden selbstständig und kann seinen Produktionsprozess optimal planen. Das Projekt begann Mitte 2006. „Nach einer Anwenderschulung haben wir unmittelbar damit begonnen, die Konsignationslager von Bosch nach der VMI-Methode zu steuern“, erzählt Kaiser. „IT-seitig verlief die Einführung reibungslos und weil wir vorab unsere Geschäftsprozesse genau analysiert haben, konnten sowohl unser Kunde als auch wir aus dem Einsatz der Lösung einen unmittelbaren Nutzen ziehen.“ Die Lagerdisposition nach dem VMIAnsatz ging mit einigen grundsätzlichen Veränderungen einher. So wurde die Fläche des Konsignationslagers um zwei Drittel reduziert, was auf beiden Seiten zu Kosteneinsparungen und positiven Effekten auf das Umlaufvermögen geführt hat. „Früher standen uns bei Bosch entsprechende Lagerflächen zur Verfügung, für die wir jedoch bezahlen mussten“, sagt Kaiser. „Durch die wesentlich verbesserte Produktionsund Lieferplanung brauchen wir diese Flächen heute nicht mehr.“
Niedrigere Kosten, höhere Planungssicherheit
Die Basis für Kosten- und Prozessverbesserungen bildet die neue Dispositionsmethode. „Wir sind heute frühzeitig über die Bedarfe unseres Kunden informiert und können Produktionsprozesse und Kapazitätsauslastung viel genauer planen“, erklärt Kaiser. Dank dem VMI-Ansatz kann das Unternehmen die Liefertermine und Losgrößen selbst bestimmen und Lieferungen bündeln. Das macht sich vor allem an der Transportfrequenz bemerkbar: Musste früher täglich geliefert werden, reichen inzwischen ein bis zwei Fahrten pro Woche aus – was massive Kosteneinsparungen ermöglicht.Auch die Anzahl der Sonderfahrten hat sich stark verringert, denn SupplyOn gewährleistet eine genaue Bestandsüberwachung und informiert den Lieferanten rechtzeitig über drohende Engpässe. „Während wir beim klassischen Lieferabruf lediglich über Termine und Mengen informiert werden, kennen wir beim VMI-Ansatz die tatsächliche Lagersituation und können frühzeitig auf kritische Entwicklungen reagieren. Die größere Eigenverantwortung, die wir als Lieferant tragen, und der Einblick, den wir in die Bestandssituation des Kunden haben, ist deshalb für beide Seiten von großem Vorteil“, sagt Kaiser. „Wir können prozesskosteneffizient und vorausschauend produzieren und liefern. Unser Kunde profitiert dabei von einer hohen Versorgungssicherheit.“ Im nächsten Schritt soll eine Schnittstelle zwischen SupplyOn und dem bei Franz Wolf eingesetzten PPS-System für eine vollständige Integration und Automatisierung des gesamten Prozesses von der Produktionsplanung bis zur Verwaltung des Konsignationslagers sorgen. Kaiser rechnet damit, dass dann weitere Rationalisierungspotenziale realisiert werden können.
Ein wichtiger Beitrag zur Wettbewerbsfähigkeit
Petra Kaiser sieht den Einsatz von SupplyOn jedoch nicht nur aus der Perspektive der Kostenreduktion und Planungssicherheit. „Als kleines Unternehmen in einem globalisierten Markt müssen wir unsere Position durch Qualität, Flexibilität, Zuverlässigkeit und Innovation sichern, denn einen reinen Preiswettbewerb werden wir nicht durchstehen“, erklärt Kaiser. „Der Einsatz digitaler Prozesse ist heute eine Voraussetzung für Transparenz und Aktualität der Informationen und ein zentrales Werkzeug für eine nachhaltige Prozessoptimierung. Innovative Prozesse wie Vendor Managed Inventory fördern die enge und produktive Zusammenarbeit mit unseren Kunden. Sie sind für uns deshalb ein essenzieller Beitrag zur Zukunftssicherung.“
Weitere Case Studies zu Vendor Managed Inventory
Case Study im PDF-Format zum Herunterladen
Sie möchten mehr Informationen über Supply Chain Collaboration erhalten?
Geben Sie einfach Ihre Kontaktdaten ein und wir werden uns so schnell wie möglich mit Ihnen in Verbindung setzen.