Bosch Next Generation Transport Management – an award-winning project
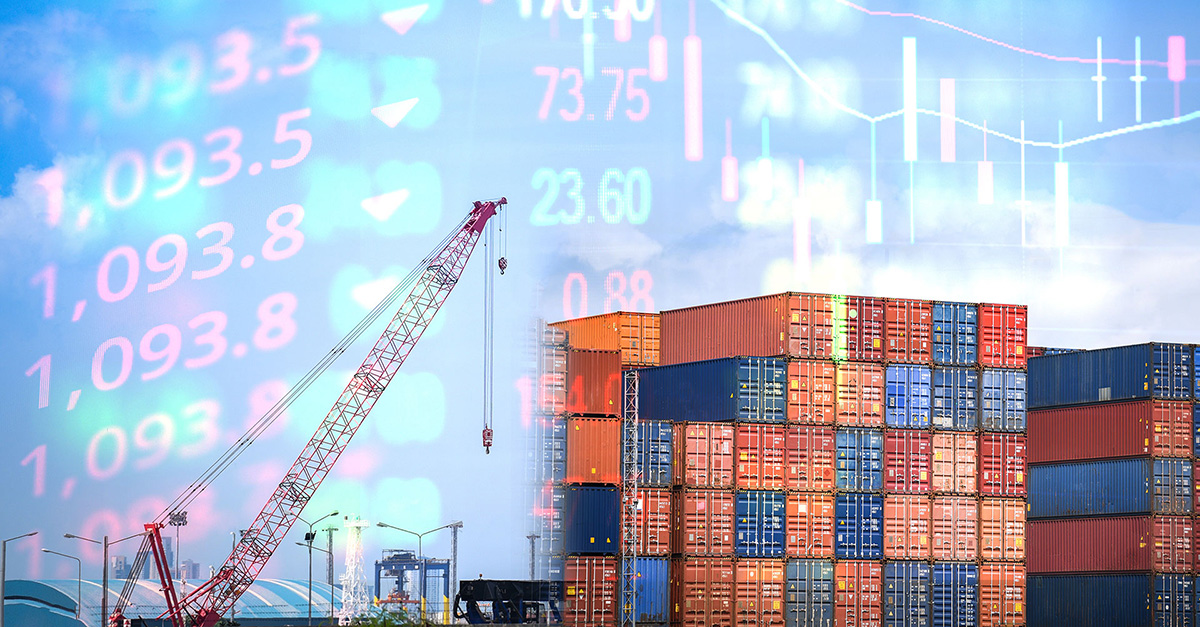
The global automotive supplier Bosch has set the goal of realigning its inbound transport management worldwide and making it future-proof. The main reason for this realignment was the enormous savings potential that can be leveraged by a seamlessly integrated inbound transport procurement and transport process.
The basis of this future-oriented project, “Next Generation Transport Management”, is the interaction of SupplyOn’s Supply-Chain-Collaboration-Solution (SCC) with Eurolog’s Transport Management System (TMS): The integration of the two innovative solutions, coupled with professional rollout and project management, were the basis for successful implementation. The decisive factors for success were also the strong management on the customer side and the team’s full commitment. The project 2024 has been recognized with the VDA Logistics Award and is therefore one of the flagship projects for the industry.
What is the Next Generation Transport Management about?
The Next Generation Transport Management project has made a high degree of process complexity in supply chain and transport management more manageable via one central platform. This platform connects thousands of players – production plants, suppliers and logistics service providers – and brings benefits for all parties involved. The most important advantages are massive savings in costs and CO2 emissions. In addition, a 30-40 percent increase in efficiency has been realized in the administrative area through seamless shipment tracking and automated processes in incoming and outgoing goods.
These savings have been achieved through a seamless process from the material requisition note to the supplier, through the supplier’s transport notification, to Bosch’s transport order.
The processes in detail
The supplier receives the material demands from Bosch via delivery call-off or single purchase order via SupplyOn. On the basis of such a demand notice, the supplier registers the transport requirement via a so-called forwarder pickup advice, or FPA for short. It is important to note that the supplier merely advises the transport, but does not order it. Bosch itself places the actual transport order in the TMS through the system.
The FPA message contains all the information necessary for the transport, typically which material in which quantity, how packed, where and when it should be picked up and sent to where. For certain materials, additional detailed packaging instructions can be stored in the system. These contain, for example, information about packaging units with dimensions and weight, label numbers and much more.
Before Bosch actually places the transport order, the FPA data is transferred via an interface to the Eurolog transport management system. The TMS consolidates several FPAs into loads and determines the most cost-effective carrier. The transport is then ordered on this basis.
To further optimize the process, the existing solution was further developed during the course of the project and adapted to the specific needs of Bosch. This includes, for example, a cross-system exchange of route information that can be used to automatically determine the best possible transport, taking into account predefined routes. To do this, a logic was developed that takes into account the predefined routes in the SAP system’s requirement notification. Based on the information from the material requirements planning in SAP and the route information, Bosch already notifies the supplier of the ideal pick-up and arrival date with the material requirements message.
When the supplier enters its transport notification, a check is run in the background to see if the date requested by the supplier is feasible. This automation eliminates the need for manual coordination between Bosch and the supplier. This automated interaction with the SAP system is a real game-changer in transport management and has been implemented here for the first time.
Fast rollout
The system went live in August 2022, triggering the mass rollout. The speed with which Bosch and SupplyOn’s rollout team activated the so-called networking links, i.e. the connection of a supplier to a specific Bosch plant via SupplyOn, is impressive. In just 12 months, for example, around 3,500 connections were realized via which more than 15,000 FPA messages are sent per month.
Key success factors
A success that has many factors: In addition to the already mentioned strong management on the customer side and a strong commitment of the entire project team to make the project fly despite all the complexity, another success factor, as banal as it may sound, is the quality of the master data: Which supplier is relevant for the new process? Which DUNS number does he have? Who is the right contact person? Which plants does this supplier deliver to? What is the control point ID? Bosch impressively created this basis in just a few months.
This project also showed that a TM project is primarily a change management project rather than an IT project. An estimated 90% of the project work is coordination and communication, with a maximum of 10% being coding and configuration. This is an aspect that is often underestimated. Moderating and supporting this change management is one of the strengths that Eurolog and SupplyOn have jointly exploited here in their interaction with their long-standing customer Bosch.