Bosch Thermotechnology China improves its inventory management capability with SupplyOn
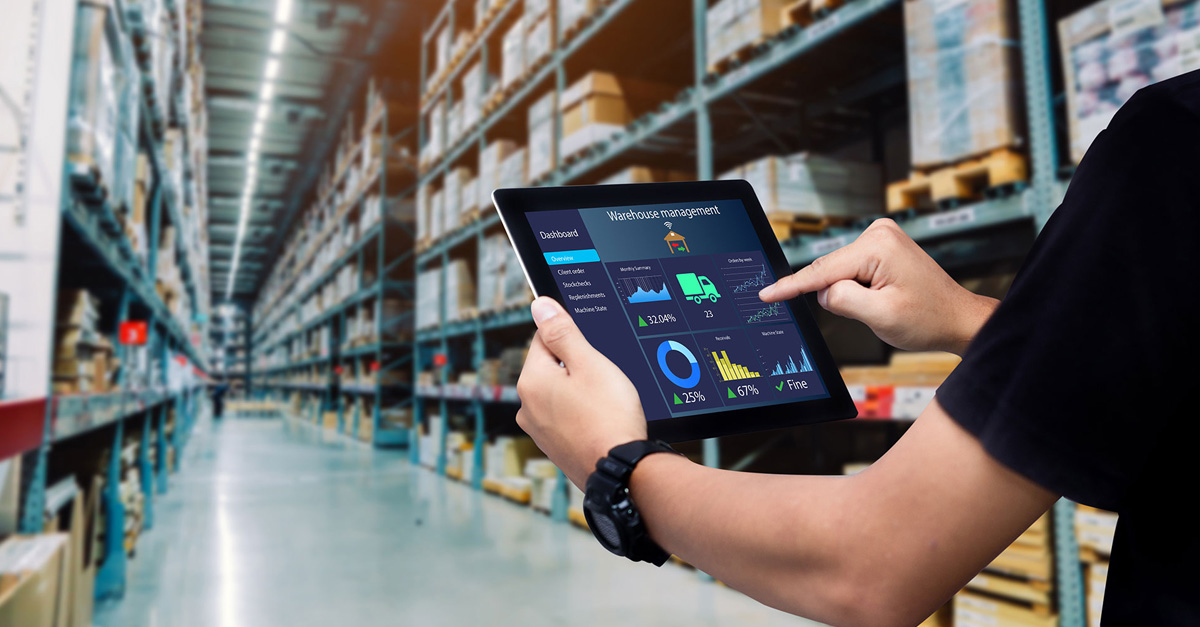
Bosch Thermotechnology provides all activities involving heating technology and hot-water solutions. Bosch Thermotechnology has a number of major international and regional thermotechnology brands and supplies people with state-of-the-art technologies worldwide. In times of scarce energy resources, the topic of efficient heat generation is of existential importance. Innovations from Bosch Thermotechnology have been setting trends for centuries.
As a buyer company, Bosch Thermotechnology is constantly exploring the efficient digital collaboration, in order to realize the fastest delivery speed, lower logistics cost and higher product quality throughout the whole supply chain.
Vendor Managed Inventory (VMI) is a management strategy that aims to obtain the lowest cost for both the buyer and the suppliers, by setting the maximum/minimum inventory level in a mutual agreement to let suppliers manage the inventory. SupplyOn’s VMI provides Bosch Thermotechnology in China with a mature system to address these challenges. With the completion of the project in August 2022, an important milestone has been reached that represents a major leap ahead for Bosch’s information management.
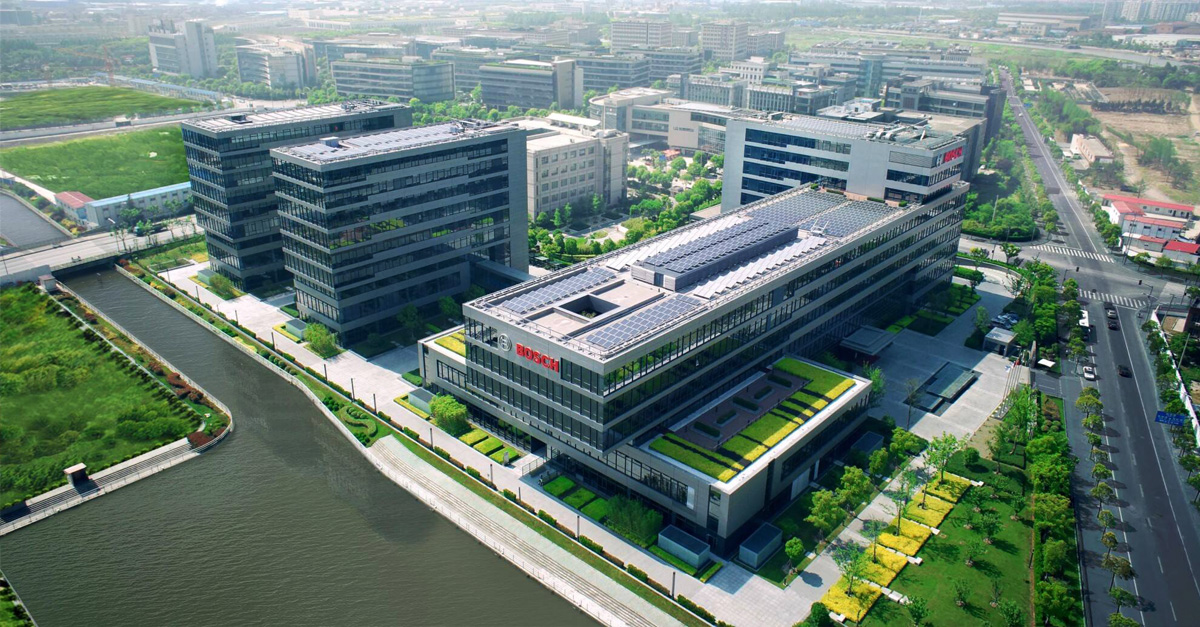
End-to-end VMI management
Before the SupplyOn VMI project was launched, Bosch Thermotechnology and its suppliers in China faced some problems, such as missing or delayed information at logistics control points, or supplier performance monitor difficulties. The VMI solution provided by SupplyOn helps Bosch Thermotechnology China to recognize the existing and potential business pain points, and then offers reasonable actions.
- End-to-end Management: SupplyOn VMI receives master data and business data from the ERP. Suppliers creates planned receipts and ASN on the SupplyOn platform, and send the delivery information back to the ERP.
- Inventory Monitor: According to the daily inventory, demand and planned receipt, VMI automatically calculates the projected inventory. Once the actual or projected inventory exceeds the maximum or minimum inventory level, the system will send an early alert to both Bosch and the supplier to notify the supplier of timely replenishment and explain the reason to Bosch.
- Alert management: Apart from inventory alerts, the VMI system also provides ASN alerts. When the actual delivery quantity and arrival time are inconsistent with the ASN’s planned quantity and time, the system will also automatically send the alert email to notify Bosch and its suppliers to find and solve the problem in time.
- Replenishment Method: Both Inventory Projection (IPR) and Replenishment Planning Monitor (RPM) are supported. For the IPR process Bosch sends an inventory report and gross demand messages. Based on this information the projected inventory is calculated and displayed over time. For the RPM process Bosch sends inventory report messages and the suppliers create the ASNs based on today’s inventory and agreed Min/Max inventory level.
- Supplier Performance Monitor: Development of a performance assessment form exclusively for Bosch, with which users can analyze the VMI consignment supplier lifecycle based on suppliers, time range, product categories and other dimensions.
Key factors of project success
The right suppliers and materials are critical elements for the success of a VMI project.
The suitable suppliers:
- Supply Chain Management Capabilities: For suppliers who have little production capacity or poor production plan execution ability, even if the SupplyOn VMI automatically calculates the replenishment quantity and delivery time, suppliers still cannot follow the process.
- Long-term partnership: Consignment suppliers typically have a close relationship with Bosch. When consignment suppliers implement the VMI system, they will be responsible for the inventory management and ownership. So Bosch has the obligation and confidence to provide the consignment suppliers with core business data such as demand and inventory.
The suitable materials:
- Relatively stable demand: when buyer’s demand fluctuates greatly, the bullwhip effect is then produced, which will cause great pressure on the supplier’s replenishment plan.
- High demand frequency: For products with low demand frequency, using Excel to manage supplier replenishment has the higher input-output ratio than using VMI.
The benefits
- End-to-end transparency of supplier inventory management
- Reduced transportation costs
- Early warning of inventory risk
- Cost savings through lower inventory levels
Customer review
The SupplyOn VMI solution is an intuitive supply chain platform based on a global business network. This provides maximum support for Bosch Thermotechnology and its suppliers in a more efficient digital collaboration.
At the same time, we also want to thank the SupplyOn project team. During the implementation of the project, both teams communicated and collaborated closely, overcame the impact of the pandemic and the difficulties of the project. The entire team worked in a very professional and dedicated manner.
— WANG Yukun, Project Manager, Bosch Thermotechnology China