Digitizing Repair Orders: a game-changer for efficiency and customer satisfaction in the aerospace industry
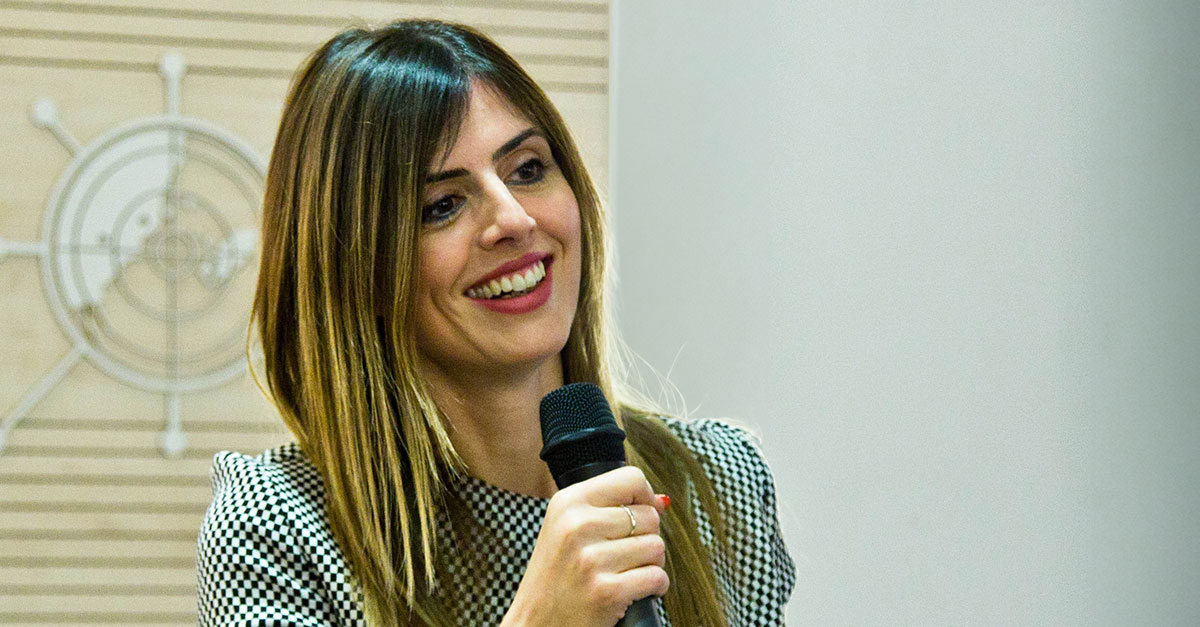
In a dynamic industry like Aerospace and Defense, where precision and efficiency are paramount, every process counts. And one of these processes is the management of non-operational parts that cannot be installed in an aircraft or helicopter due to a need for revision, repair, overhaul, or the like — the so-called Repair Orders & Overhaul (R&O).
Leonardo, a major aerospace, defense and security company, set out to fill the gaps to efficiently manage the specifics of this process, seamlessly integrated into a digital platform. But what really sets this endeavor apart is the idea of community. As part of the BoostAeroSpace community, Leonardo and another major aerospace OEM joined forces to transform the repair and overhaul ordering process for the benefit of the entire community as a pioneering co-leadership initiative.
We sat down with Angela Marotta, Project Manager for AirSupply at Leonardo, to learn more about this extraordinary initiative and how Leonardo is benefiting from the new process:
Repair Orders — a critical process in the aerospace industry
Angela, could you please describe the role that repair orders play in Leonardo’s business, how they have been managed in the past and what the limitations have been?
The Repair and Overhaul process is a critical part of our strategic management and our customer services business, especially in our Helicopters and Aircraft divisions. We handle around 7,000 Repair Orders for Aircraft and 32,000 Repair Orders for Helicopters (for 1 year), involving about 600 suppliers. The process has four key steps: publishing, collaboration, acceptance, and execution of Purchase Orders (POs).
While it all boils down to PO management, the first three steps have some unique characteristics when handling POs for R&O. These specifics were not fully covered by our previous solution. As a result, we had to manage some or all of these process steps outside of the portal.
With a new and dedicated R&O process we wanted to increase the traceability of logistical movement of unserviceable parts, track negotiations, incorporate supplier quotations and enhance the status visibility of the R&O flow in general.
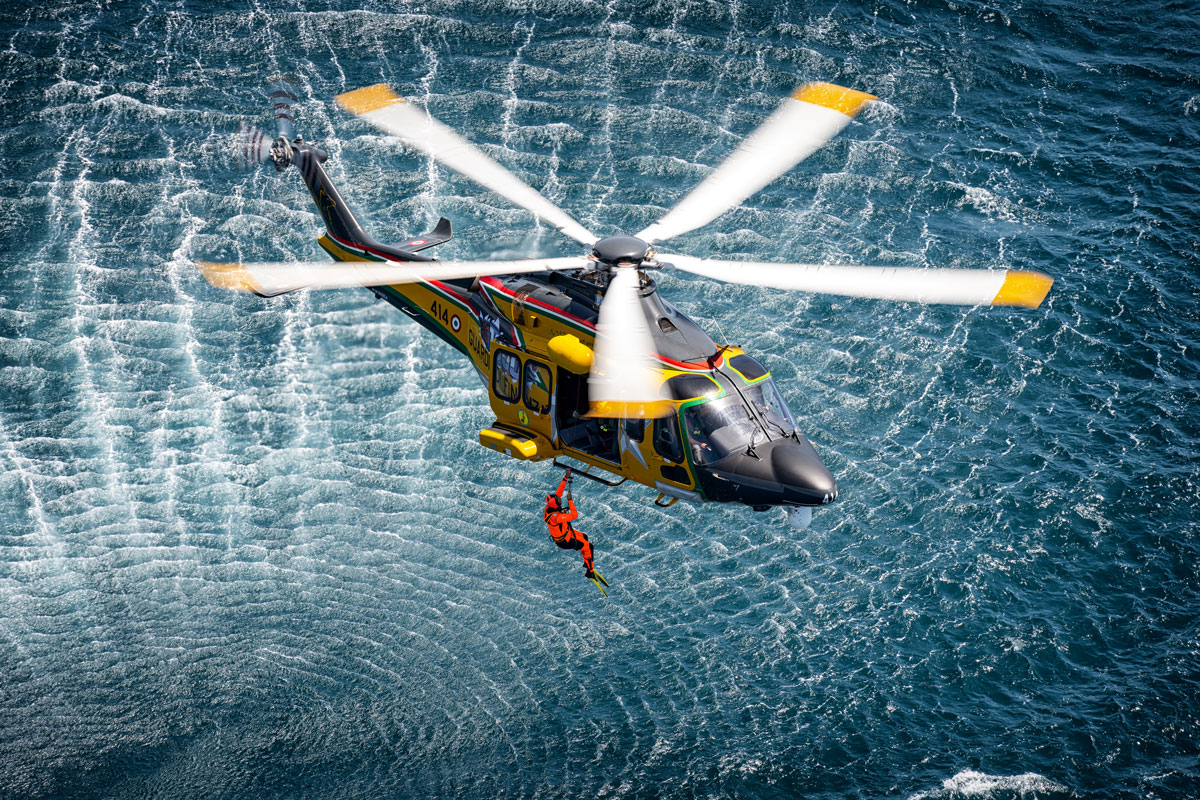
It’s fascinating to see the scope of the challenge, Angela. Why did Leonardo choose SupplyOn to address these issues?
Our decision is in line with our company-wide strategy to use a single portal to collaborate with our suppliers on supply chain processes. And since 2017, this portal has been AirSupply by SupplyOn, the leading solution in the aerospace industry.
Joint project for an industry-wide issue
How did this initiative to transform the management of Repair Orders become a joint project with another major aerospace OEM?
When we selected in 2016 and implemented AirSupply to harmonize and advance our supplier collaboration on a group level, we also joined the BoostAeroSpace community in 2017. All community members are like-minded, innovative aerospace companies using this comprehensive, industry-specific supply chain solution.
So, naturally, we discussed with both, SupplyOn and BoostAeroSpace, how we could extend AirSupply to support this process, both for our existing suppliers and for new ones coming on board. After all, the Repair and Overhaul process is a critical aspect of aerospace and defense. It follows the same rules for customers and suppliers across the industry. Customer support and service are paramount, and efficiency is essential for all.
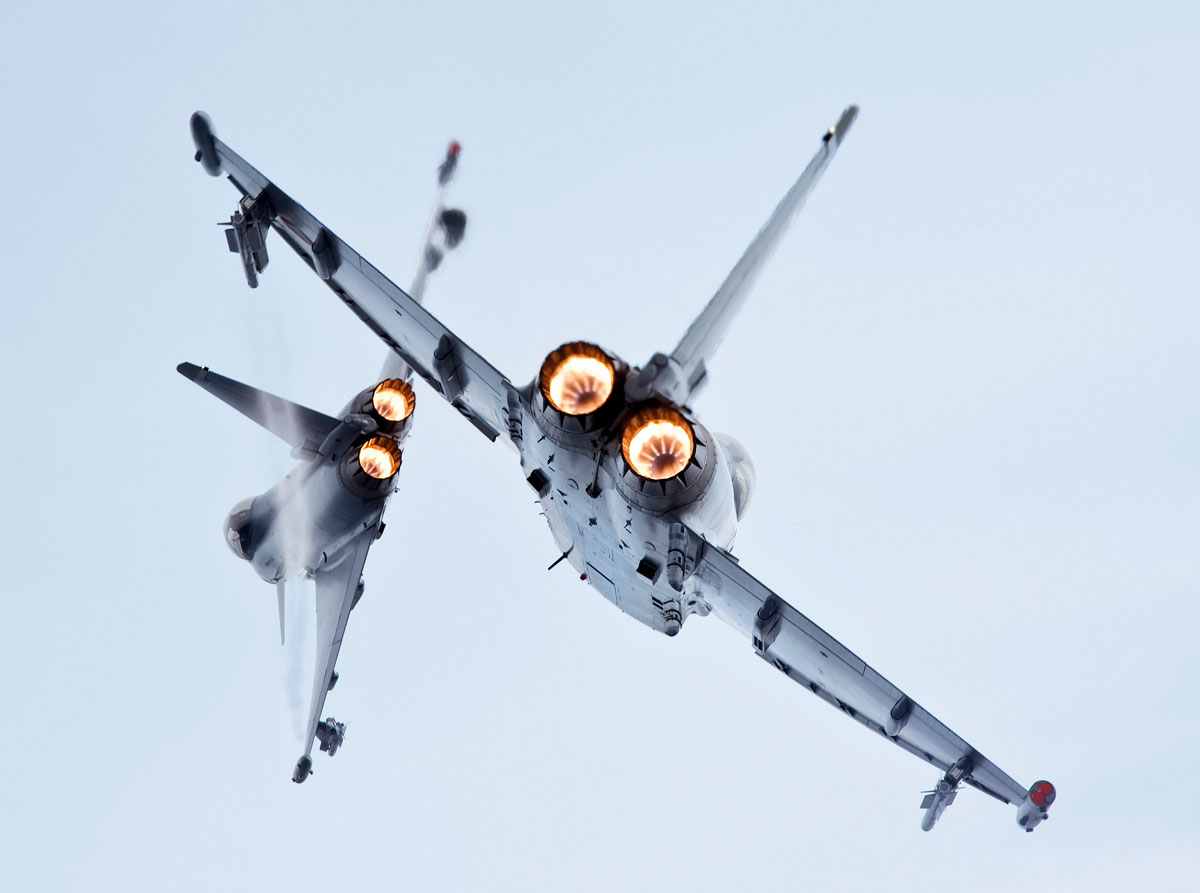
During these discussions last year, in 2022, another major aerospace OEM expressed great interest in transforming and integrating this process into AirSupply. We decided to work closely together on requirements, solution design, cost and testing. The very first co-leadership project among the BoostAeroSpace community members was born! Our common goal was to add value to the platform by implementing this key functionality for the aerospace and defense industry.
For us at Leonardo, this project was a great opportunity to demonstrate our community and collaborative spirit: Internally, by aligning all of our business units around the request and identifying common requirements. And secondly, within the community, to verify how such a pioneering co-leadership initiative can become a great success.
What are the essential elements required of a successful co-leadership project?
Transparency in sharing information about common processes is key. But you also need an open-minded approach to solution design and a deep understanding of the impact of the process on all internal stakeholders. Last but not least, continuous collaboration with the procurement and customer support departments across all business units was critical to the success of the project.
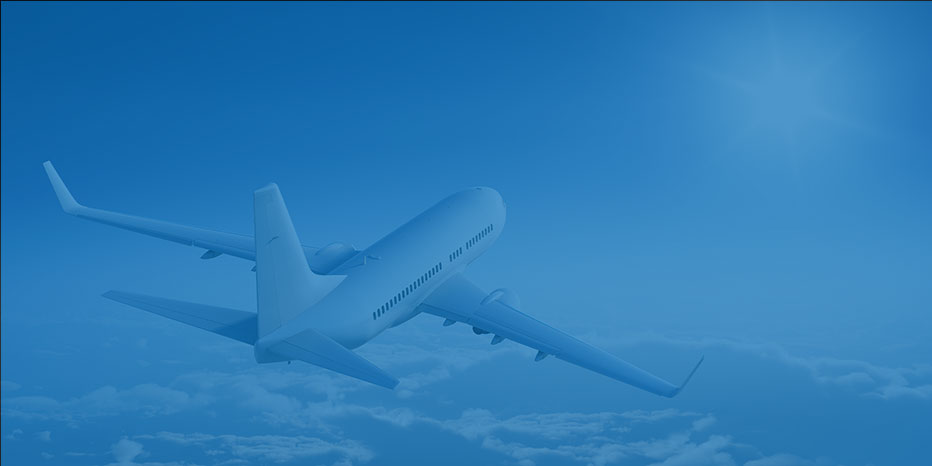
Project progress at Leonardo
What is the current project status at Leonardo?
The Repair and Overhaul Process solution has been released on AirSupply in April 2023 and is already up and running for the Helicopters Division since June 2023. We’re currently working on the integration with backend of the Aircraft Division backend. This is set to be released in November 2023. The integration with the Electronic Division is then planned for 2024.
Leonardo’s onboarding policy is to enable all existing suppliers to use the new process and to take the opportunity to onboard new Repair Order suppliers.
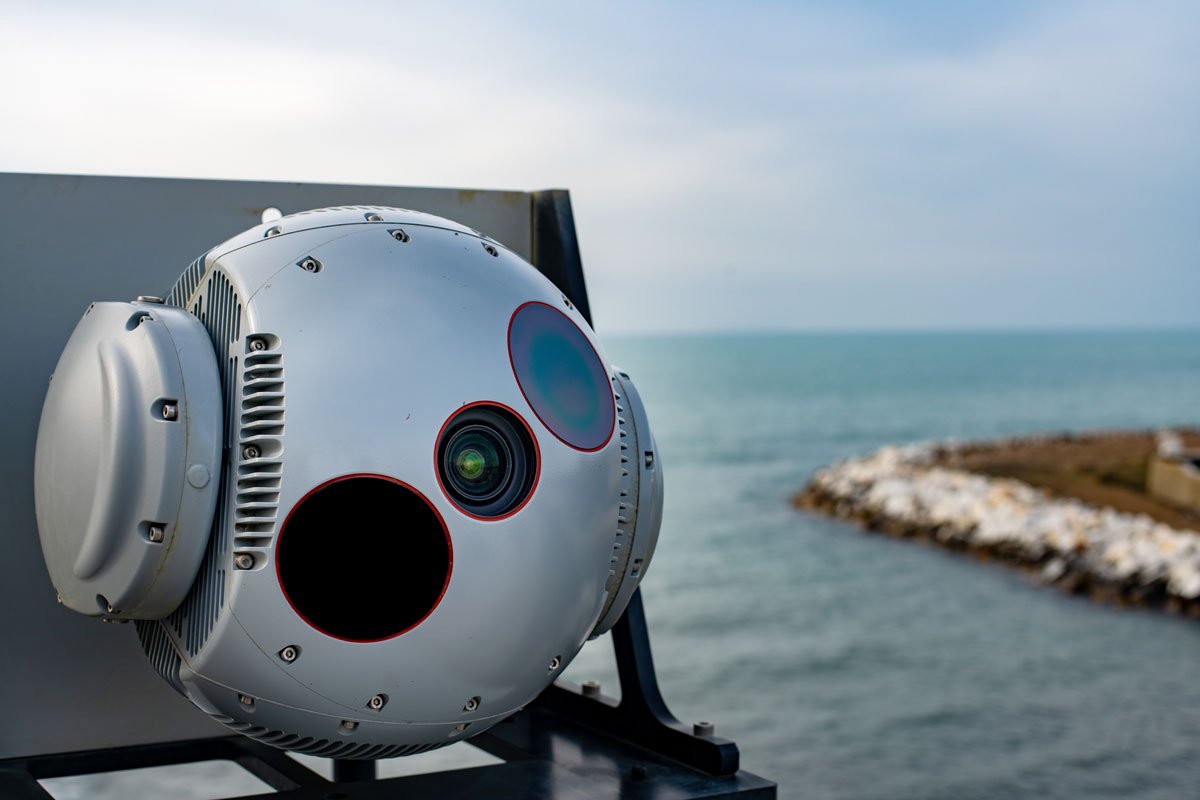
Can you tell us how this project has helped to address your initial issues, Angela?
With the new Repair and Overhaul process, Leonardo aims to accelerate procurement time-to-market, ensure on-time payments, and improve cost efficiency in our Customer Services business. It aligns with our company’s success drivers, which include digitalization, traceability, efficiency, standardization, and supplier collaboration.
And what is next for this project, is there still work to be done?
The solution released in April 2023 is only a first version. We have additional requirements planned for development in 2024. In the meantime, our goal is to expand the supplier perimeter and extend the solution to all Leonardo divisions.
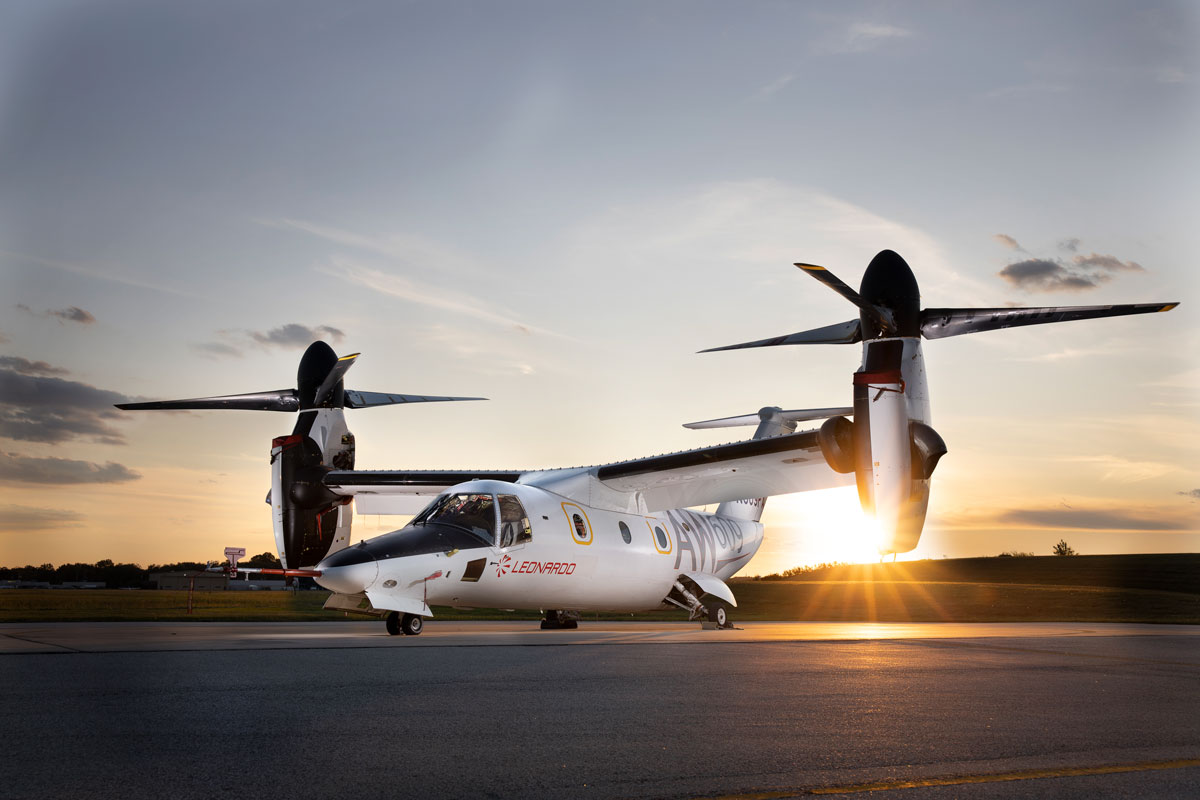
Community collaboration as driving force for innovation
How do you think you can influence your fellow community members to adopt this process in their organizations? What are your plans here?
All BoostAerospace community members meet every year in a different location for a “Customer Day”. At last year’s Customer Day in Paris, we jointly presented our initiative together with the other participating aerospace OEM. During this presentation, we demonstrated how this solution enhances the AirSupply suite of functionalities.
Technically speaking, we have implemented a set of enhancements that complement the existing Purchase Order process, allowing users to access dedicated screens to efficiently manage Repair Orders.
This way of working has proven that new processes can be implemented efficiently while minimizing the risks of regression to the existing core process.
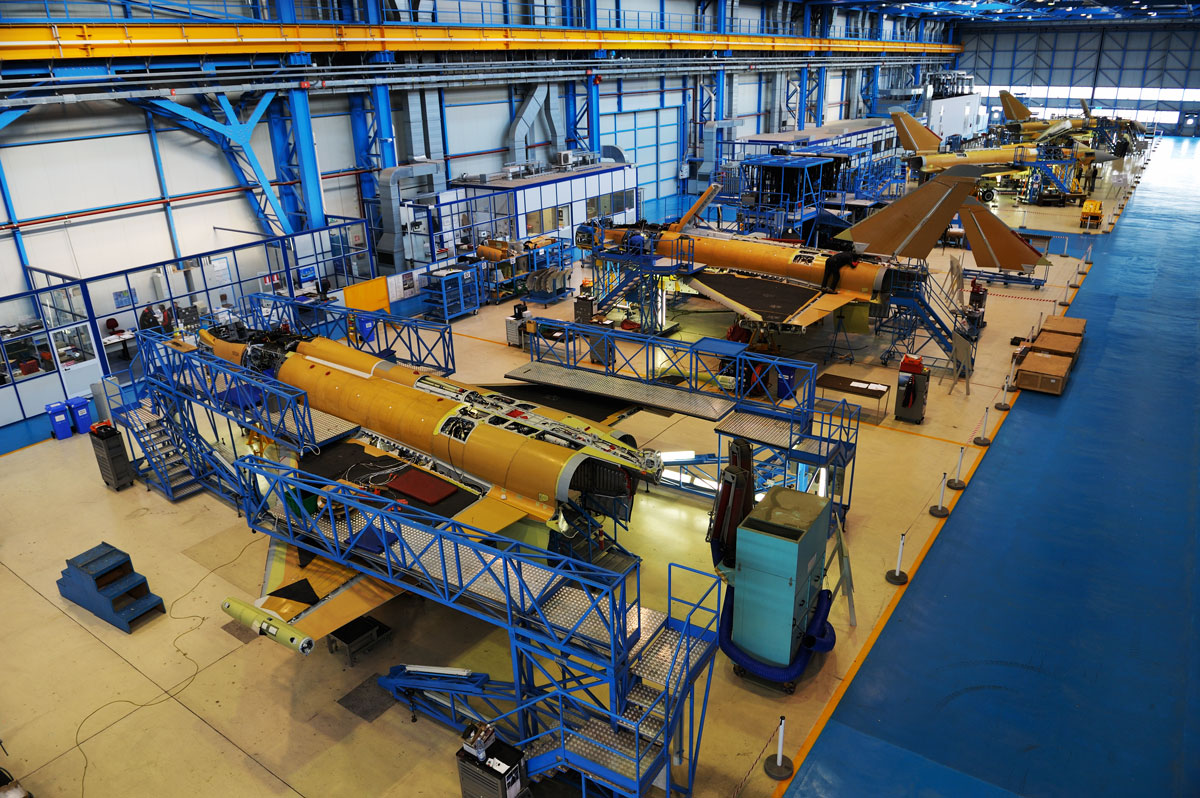
Angela, looking back, how vital is collaboration in the community for a successful solution?
Collaboration with the community and with SupplyOn is the key to success for Leonardo. The exchange of information, comments, and different perspectives ensured that we found an efficient and smart solution.
Most importantly, this project has been a valuable lesson for the community in terms of working together on project management and addressing requirements in innovative ways.
Are there additional points you would like to see the community tackle in the future?
Yes, we’ll be discussing additional requirements related to report management for the Repair and Overhaul process and to fine-tuning the solution for quote management.
One last question, Angela: do you have any other plans for how you’d like to develop supply chain management at Leonardo that you can share with us?
Absolutely. At Leonardo, we believe in sharing our needs with the community to further improve the platform. How to make it even more user-friendly and attractive for suppliers is an ongoing discussion, and we’re eager to collaborate to achieve that.
Thank you, Angela, so much for your valuable insights! Looking forward to seeing these plans come to fruition in the coming years. All the best to you and your projects.