Inbound transports: boost transparency and efficiency with fully automated transport notification
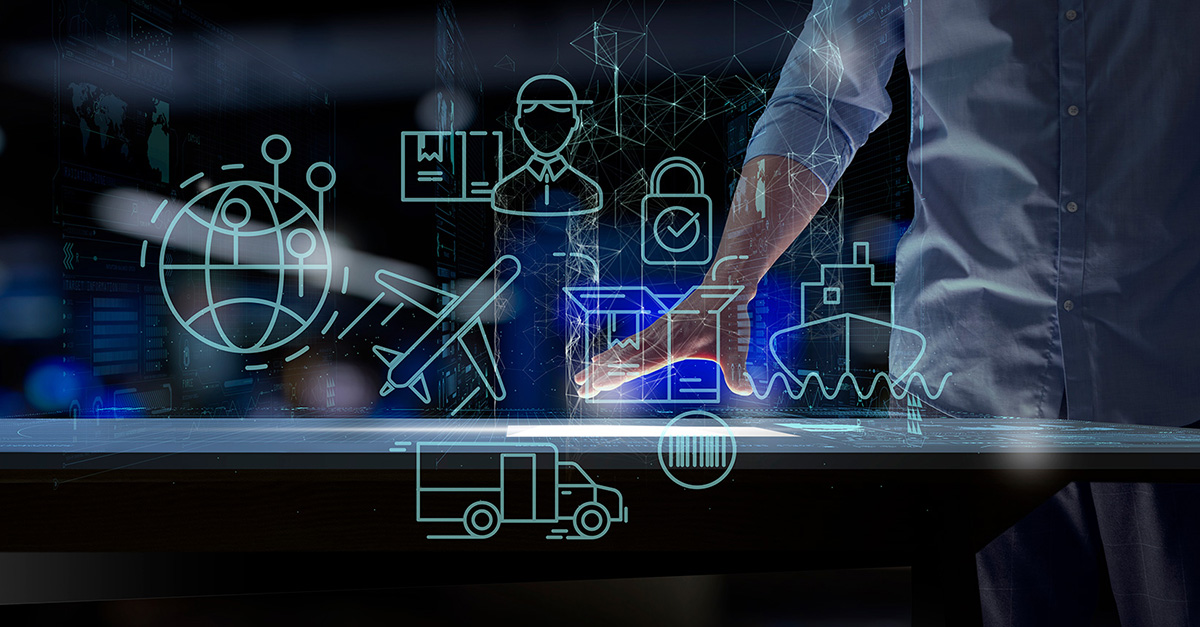
The sharp rise in energy prices has a direct impact on transport costs. Especially now, it is extremely important to exploit all available savings potential. Bundling of transports, high utilization of loading capacities and timely transport notifications are important levers to keep the price explosion under control. In addition, reduced inventories demand secure, monitored transport handling to prevent delays from leading to costly production losses.
This means logistics managers need not only immediate, i.e. real-time, information about delays during transport. Moreover, they need quick answers to questions such as: “Which materials are affected by the delay?” Or: “What was damaged during transport?”
Material reference is essential
The key to monitoring inbound shipments and, at the same time, saving costs, lies in the transport notification by the supplier. If this is not done on time or does not include the material reference, additional costs are incurred. Tracking & tracing of the transports is then only possible with considerable manual effort.
Fully automated transport notification
A fully automated transport notification (Forwarder Pick-up Advice, FPA for short) with direct reference to the ordered materials and quantities provides a remedy. SupplyOn utilizes the electronically stored purchase orders or delivery schedules for this purpose. Based on this information and the recorded transport times, the solution calculates all the necessary time stamps, such as the notification, pick-up and delivery dates. Alternatively, transport times can also be transmitted electronically.
The system then generates optimized and bundled transport notifications, automatically packs the materials while generating unique package numbers for picking, and transmits the data to the Logistic Service Provider (LSP) defined in the system. The supplier has full control over the process and can independently configure the degree of automation — with or without automatic packing.
Creation of delivery documents made easy
The package labels required for clear identification of the materials is available for printing in advance from the transport notification and attached to the containers. With just one mouse click, you can convert the transport notification into an Advance Shipping Notification (ASN) and forward it electronically to the parties involved in the process. The decisive factor here is that the entire ordering, delivery and transport process is mapped end-to-end and, in the event of transport discrepancies, the system immediately identifies which materials and quantities are affected.
Prompt alerts on process deviations
The SupplyOn platform hence monitors the entire delivery and transport process and continuously checks for deviations. Should any be detected, the process participants are notified immediately. This leads to a completely transparent process chain, from loading to transport and, if necessary, customs clearance, right through to goods receipt.
Standardized information transfer
A standardized EDI interface ensures the transfer of all information in the background. In addition to the SupplyOn Transport Management System, third-party solutions can also be connected. It also allows for the electronic transmission of transport-related documents, such as dangerous goods information or pro-forma invoices, to the forwarding agent.
Conclusion
Consistent digitization and automation of ordering, delivery and transport processes can significantly reduce manual activities. The integrated alert system documents the individual process steps. Transparency is established and prevents costly production downtimes. Process deviations are detected at an early stage, measures can be initiated in time and expensive special transports can be avoided.