Reduce costs: optimize production timing and quantities depending on demand and capacity
In today’s competitive economy, the efficient management of production processes is a key success factor. Companies are faced with the challenge of planning production times and quantities in such a way that they both meet demand and minimize costs. But how can this balancing act be achieved?
In this article, we look at how matching demand and capacity is the key to cost optimization and how our software solution with its powerful simulation and optimization feature makes a decisive contribution to this.
The basics: Why are production timing and quantities so important?
A company’s production is closely linked to several factors: Demand, available capacity, storage costs and delivery times. Inefficient planning can have serious consequences:
- Overproduction leads to increased storage costs and a risk of write-offs if products become obsolete or are not sold.
- Underproduction, on the other hand, causes supply bottlenecks that result in lost sales and possible damage to customer relationships.
Optimizing production timing and quantities helps to minimize these risks and at the same time reduce costs along the entire value chain.
Key factors for optimization
1.Demand forecast
The basis of all production planning is a precise forecast of demand. This includes analyzing historical sales data, taking seasonal fluctuations into account and observing market trends. Modern technologies such as machine learning and big data can make a significant contribution here by identifying patterns and correlations more quickly and accurately.
Production capacity is often limited by resources such as machines, personnel and materials. Companies must ensure that they utilize their capacities optimally without risking overtime, expensive production relocations or high machine wear and tear.
Flexible capacity models – such as shift systems or external production partners – offer scope to cushion peaks in demand.
Cost factors also play a decisive role.
Our solution: Simulation feature for flexible “what-if” analyses
The complexity of modern production planning is often complicated by uncertainties and dependencies in the supply chain. Our software solution addresses this problem with an integrated simulation feature that offers customers and suppliers alike enormous added value.
With this feature, companies can flexibly and efficiently carry out “what-if” analyses to evaluate possible scenarios:
- How does a sudden increase in demand affect the number of my alerts?
- What happens if a supplier delays a delivery?
- What production quantity minimizes the total costs for a given stock limit?
- How critical would a temporary reduction in capacity be?
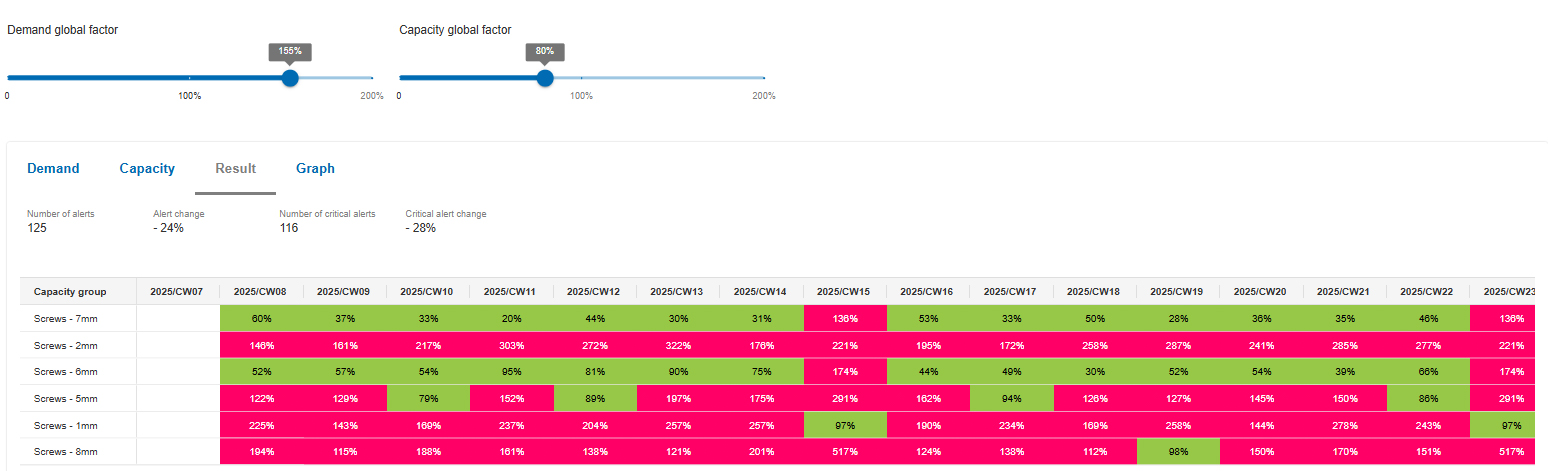
The simulation provides answers to these questions in real time. That way you can:
- Recognize bottlenecks at an early stage and take action before they occur.
- React flexibly to external influences, such as seasonal fluctuations or market changes.
- Increase efficiency by finding the optimal balance between production, storage and transportation costs.
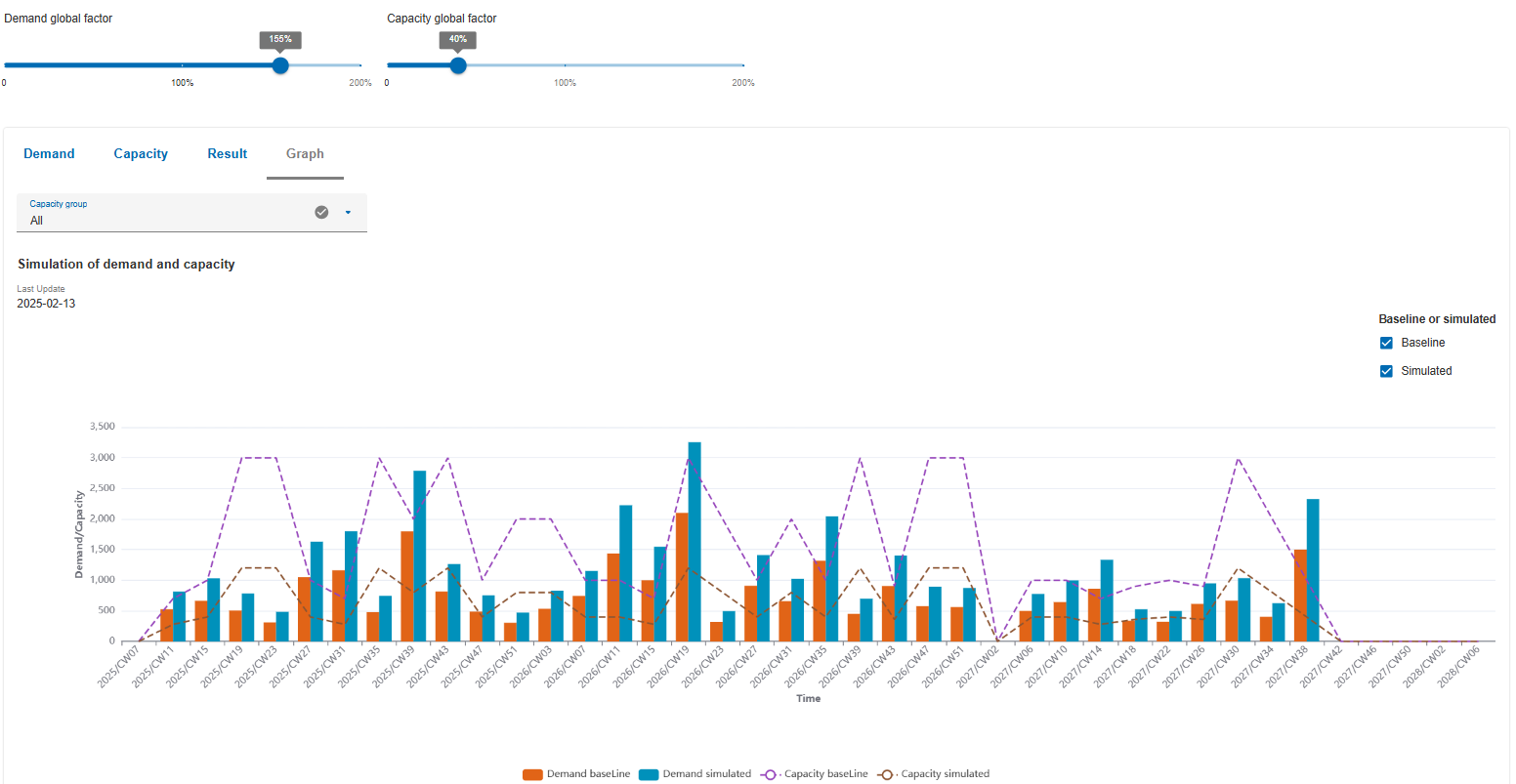
AI-supported suggestions for optimizing production planning can almost completely relieve you of the manual effort of demand and capacity planning.
The interactive visualization and the ability to share simulations with your partners bring all stakeholders together to make informed decisions and jointly develop an optimally coordinated strategy.
Based on these parameters, our tool determines optimized production planning and even provides insights into the basis on which decisions were made.