Siemens China realizes efficient inventory management with SupplyOn
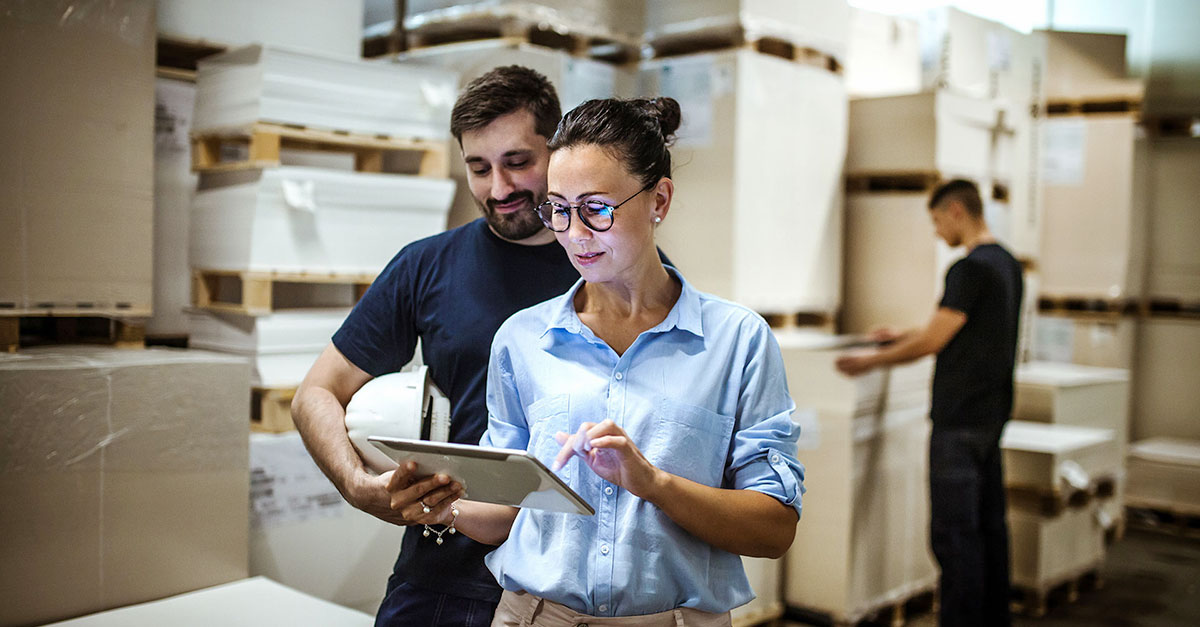
Siemens AG is one of the world’s leading technology companies. Founded in 1847, it has operations in more than 200 countries around the world, focusing on electrification, automation and digitization. Among them, the Siemens Intelligent Infrastructure Group (SI) is committed to intelligently connecting energy systems, buildings and industries, improving public life and working methods, and providing customers with one-stop, complete end-to-end solutions, covering the entire line of products, systems, solutions and services from power generation to power consumption.
SupplyOn, as a long-term important supply chain partner of Siemens, has been deeply involved in the digitization of the supply chain. With the continuous growth and change of business, Siemens Intelligent Infrastructure Group (SI) decided to replace the original Vendor Managed Inventory (VMI) system with the SupplyOn VMI module, and gradually extend it to the entire China region with two plants as a pilot.
Electronic Data Interchange (EDI) connects enterprise information upstream and downstream across Siemens’ entire supply chain, enabling closed-loop information management between Siemens plants and suppliers, improving product availability, reducing the total inventory in the supply chain, and cutting down the transaction costs of both parties.

Key factors for the successful implementation of Siemens VMI project:
- Long-standing, trusting collaboration
SupplyOn and Siemens have more than 20 years of working together on supply chain systems. At the same time, a solid foundation for the successful implementation of the project was provided by the strong support and exchange of best practices between the German management of Siemens and SupplyOn.
- Positive customer promotion
In the trial run stage, Siemens key users tried out the system in production (PRD) environment, as well as simulated the operation by the supplier. During the three-week trial operation training, the heads of Siemens plant key users also became experts in the use of SupplyOn VMI module, thus ensuring a smooth launch of subsequent suppliers.
- Efficient teamwork
After the end of the pandemic, the project teams on both sides continued to maintain efficient online communication and collaboration. Although the impact of the pandemic caused a project delay, the calm reaction of both sides has also made this experience extremely valuable.
- Customer orientation
During the implementation of the project, the SupplyOn project team fully understood the pain points and requirements of the two Siemens plants, and provided customized solutions based on customer-oriented and best practices.
The benefits
Transparent process and efficient collaboration
Suppliers can check the inventory and demand of materials in the system, create Advance Shipping Notices (ASNs) in combination with the production schedule plan and the highest and lowest stock level. The customer also synchronizes inventory information.
At the same time, the customer can also simulate the supplier’s operation to better understand the supplier’s inventory situation. In the past, timely communication was required through telephone or conference, now there is no need for additional communication time. Enterprises in the supply chain can collaborate closely based on mutual trust.
Real-time information sharing
Customers and suppliers can check the latest inventory status on SupplyOn. This significantly reduces the inventory pressure on upstream suppliers and avoids the bullwhip effect.
All relevant companies share their demand, production, sales, inventory, and other information, thus closely connecting upstream and downstream enterprises, reducing the bullwhip effect generated in the process of information transmission, eliminating information transmission errors or additional inventory caused by the safety margin of each party, and optimizing the supply chain.
Inventory monitoring and alerting
In case the actual inventory falls below the minimum or exceeds the maximum, the system automatically sends an alert e-mail to notify Siemens and the supplier. This helps to quickly find and resolve the issue.
The supplier can also set special attention to a certain material as well as regular replenishment reminders. If the demand fluctuates abnormally, the supplier can get the demand information in time and quickly adjust the replenishment strategy.
Customer review
VMI is based on a partnership of mutual trust that gives supplier the decision-making power for inventory replenishment, thus reducing transaction work such as negotiation and discussion compared to the traditional replenishment model.
The advantage of SupplyOn VMI is that it can reduce the bullwhip effect caused by the demand fluctuation of the supply chain through the sharing of the customer’s demand information. Thereby, it reduces safety stock, lowers transaction cost, and realizes an efficient supply chain coordination.
In this VMI project, we would like to thank the SupplyOn China project team and their German colleagues for helping us to solve the challenges in the project with their professional knowledge background and for providing us with a good project experience. We also look forward to further collaboration with SupplyOn in the future.
Pei, Xiaojun — Siemens Shanghai VMI plant project leader
Peng, Weihua — Siemens Suzhou VMI plant project leader