Ready for takeoff? Supply chain challenges in the aerospace industry
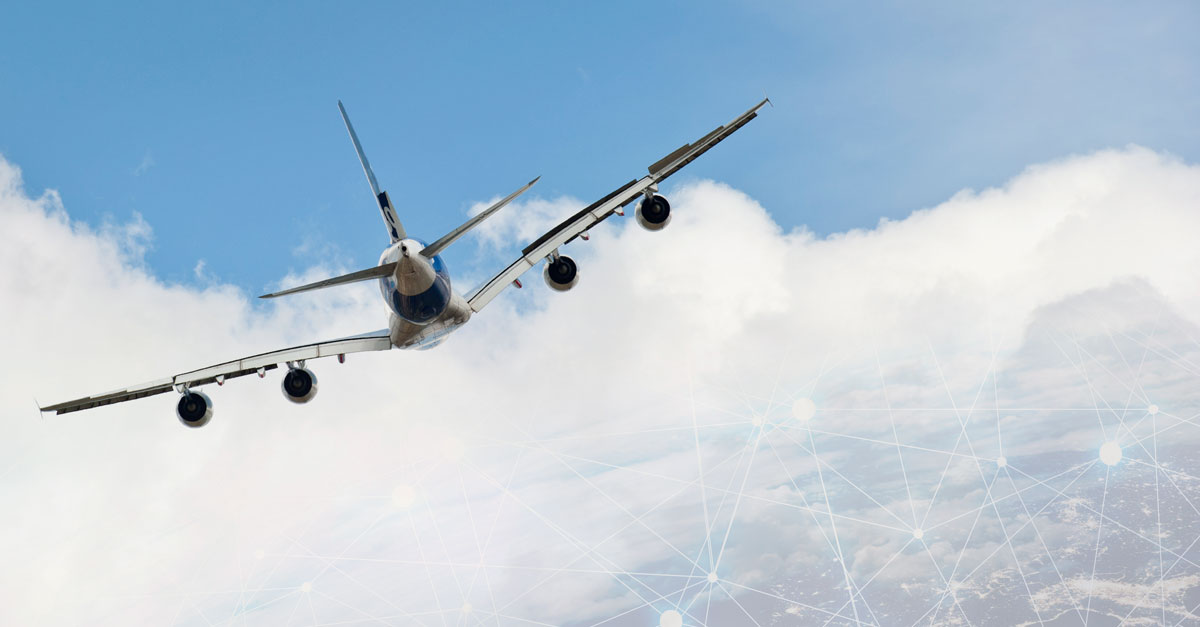
The aerospace industry has a larger international footprint than almost any other sector. Ranging from individual connectors to the completed aircraft, the supply chain often spans the entire globe. In times of ever-closer collaboration and ever-tighter deadlines, the level of digitalization should actually be extensive. Actuall.
Our recently published study presents a somewhat different picture. At least on the supplier side. This is because approximately one in three companies still work “offline”. Email, fax and telephone continue to be the most widely used means of collaboration. Another 41 percent have at least digitalized their collaboration with their customers. Admittedly, this can (and should) only be a first intermediate step. After all, those who turn a blind eye, often run into obstacles. Past experience has shown over and over again how quickly a delay in delivery right at the start of the supply chain can throw all subsequent steps into turmoil – even if the part in question is “only” a toilet door…
The problem does not lie in the suppliers’ willingness: The vast majority of suppliers surveyed want a stronger relationship with their customers and recognize the benefits of closer collaboration with their suppliers.
But perhaps because we are far from precisely this degree of collaboration at the moment, over a fifth of the companies consider themselves ill-equipped to deal with the current challenges. An assumption supported by the fact that more than one in three companies concede this to be one of the major challenges of the future.
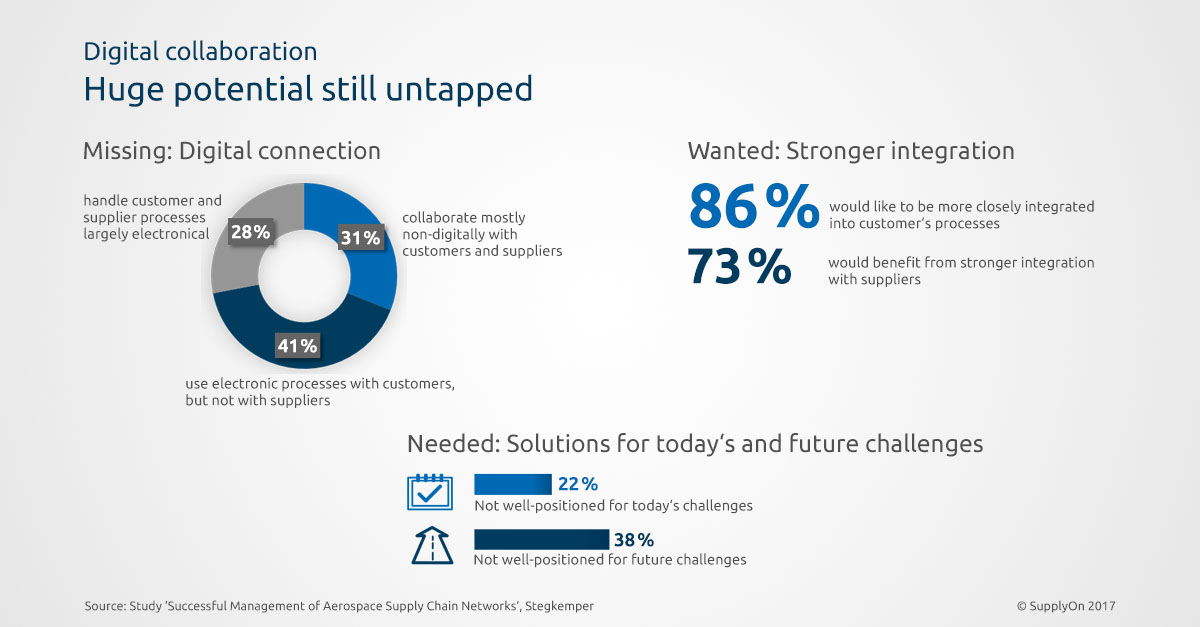
The whole is greater than the sum of its parts
Looking at the digitalization level of the individual supply chain processes is interesting. A similar picture is also repeated here. The digitalization of the outbound supply chain to the customers is considerably more advanced than to the suppliers. The greatest level of digitalization, both inbound and outbound, can be seen – unsurprisingly – in the ordering and invoicing process.
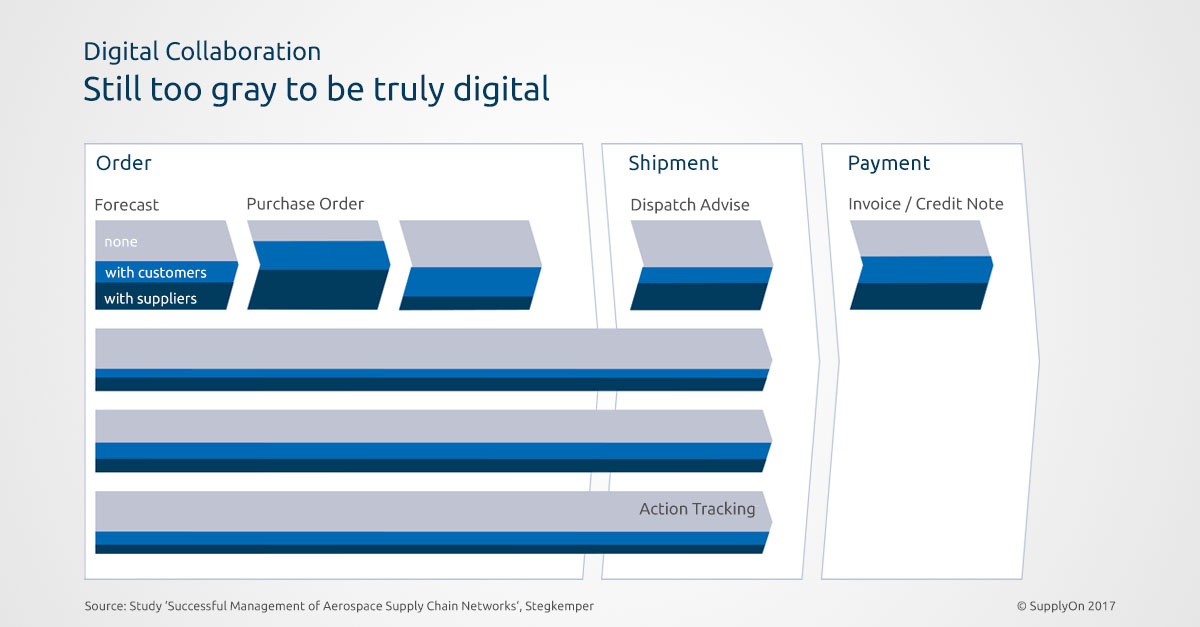
And it’s become apparent: The more complex the process (on-time delivery, action tracking, concession), the lower the level of digitalization. But it is exactly these highly collaborative processes that would most benefit from digitalization.
Which is why every small step towards digitalization is welcomed. Companies are only able to tap into their full potential if they handle all processes with their customers and suppliers within a common tool.
So what (still) causes it to fail?
When asked about the requirements for increased digitalization, the surveyed companies cited, above all, a high degree of data protection, sustainable investments, feasible running costs, equivalent transparency and analysis options. They also expressed the aim of a parties using one single solution.
The three main obstacles on the path forward were clearly identified as being a lack of pre-configured interfaces, a lack of process standards and a lack of standardization.
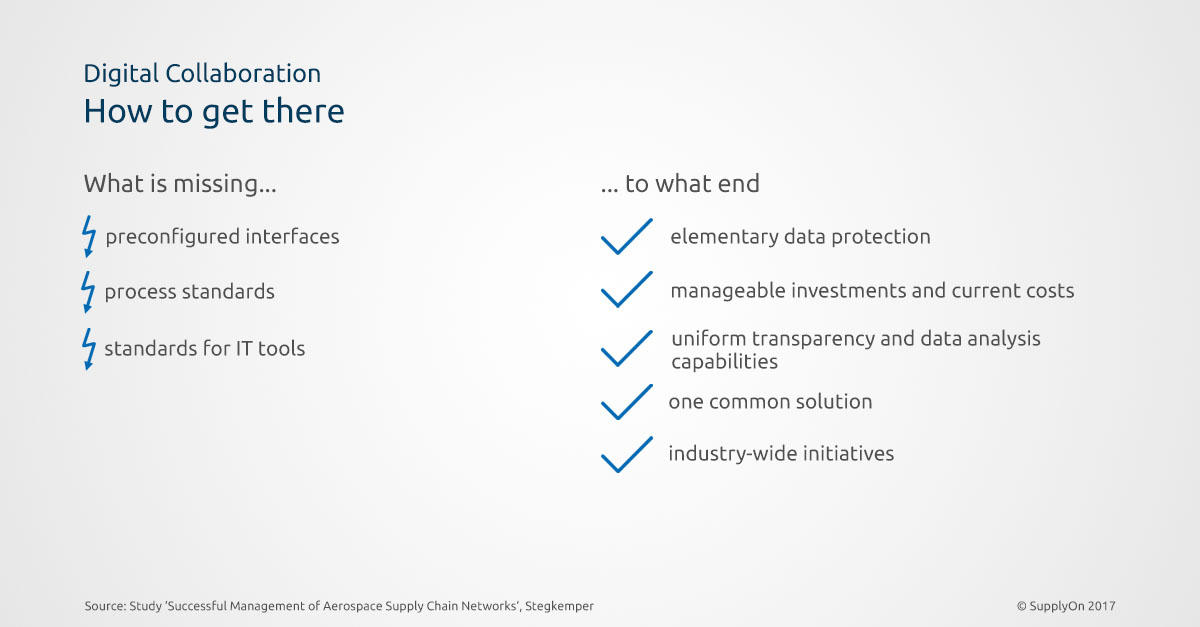
To begin with, the industry associations are called upon to support the definition of industry-wide standards. In the second step, it is the industry’s turn – above all the OEMs and Tier-1 companies – to implement and use them. The more success these have in bringing smaller suppliers onboard, the better for all. Because this then increases the visibility and responsiveness of the supply chain overall. To ensure that missing toilet doors are no longer a nasty surprise.
Request the “Successfully control complex aerospace supply chain networks” study