ZF brings in SupplyOn to gain real-time transparency for overseas transport at the material number level
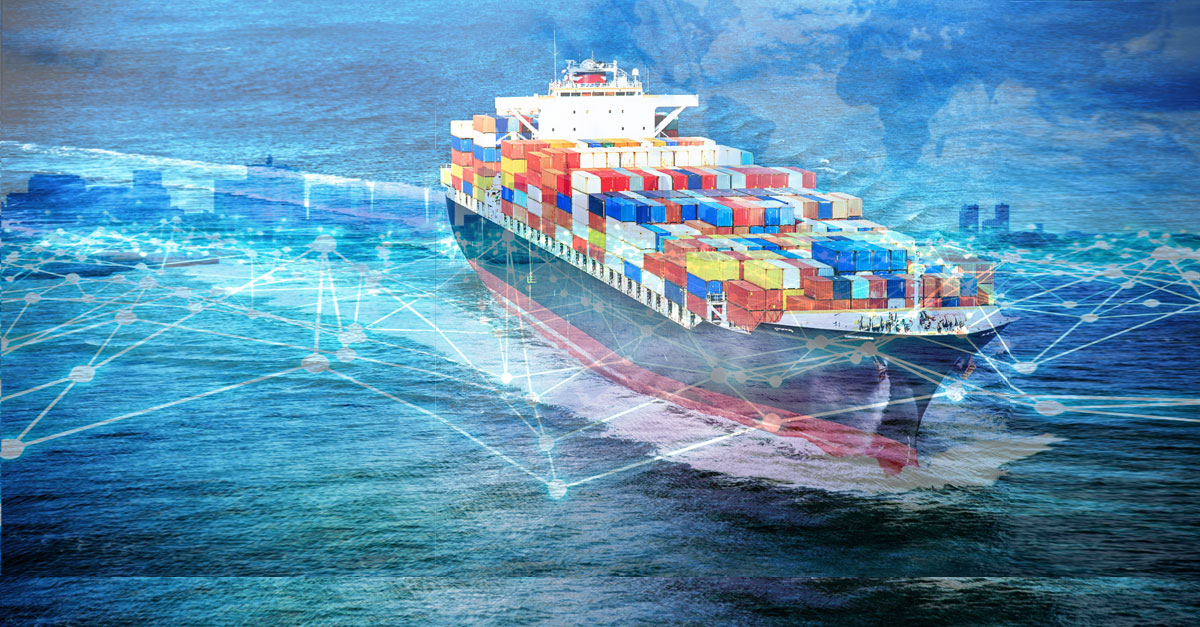
Technology company ZF provides its customers worldwide with components for just-in-sequence production. Material bottlenecks due to supply delays quickly lead to major production problems. For critical overseas transport that is prone to delays, ZF has teamed up with SupplyOn to implement a system that continuously monitors the transport status at the material level and in real-time. It provides advance notice of delays, thus ensuring stable production processes.
The challenge: High operating expenses and manual status updates in overseas transport
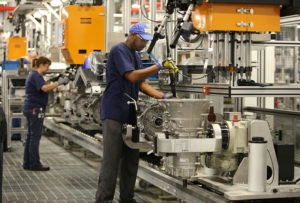
ZF Friedrichshafen AG delivers materials just-in-time and just-in-sequence (JIT/JIS) to many of its customers around the world. Exact planning of parts delivery is essential. Many of the materials are produced in Europe and then delivered for final assembly to ZF plants all over the world which, in turn, are directly linked to the customers’ plants. They are generally transported by sea, and delays are common.
During the often weeks-long overseas transport, material coordinators previously received only manually provided information via email or a service provider portal. These updates were thus never in real-time, and only at a total container level. In addition to conventional full container loads, many ZF divisions however also ship consolidated containers consisting of materials from different suppliers and ZF plants.
Consolidating the status information of individual freight forwarders, determining the material affected and reconciling it with existing supplies are time-consuming tasks for material coordinators. Material bottlenecks were often detected late. The consequences were costly special transports and adequate safety stock at the destination plant in order to prevent downtime at customer plants.
The solution: ASN tracking in real-time
ZF was looking for a solution to track overseas transports in real-time and independent of a specific forwarder or carrier. It needed to show delays immediately, while the material was still seaborne. It was particularly important to ZF that material coordinators could see the delays directly in their ERP system, without having to log in to other platforms or make separate Excel calculations.
SupplyOn was selected after comprehensive market evaluation and an initial concept from central logistics and division logistics. Implementation occurred under the project management of the Car Chassis Technology Division. Due to the number of consolidated containers, tracking at the material level was necessary and implemented on the basis of Advance Shipping Notification (ASN). Material coordinators now immediately see whether, and how significantly, they are affected by delayed deliveries.
SupplyOn integrated sea freight specialist Ocean Insights for tracking information during overseas transport. Material coordinators are informed, virtually in real-time, of delays, regardless of forwarder or carrier, and long before the ship enters the port of destination.
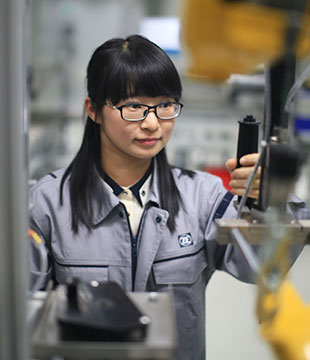
The fact that the Division boasts a uniform global ERP system gave the rollout a big boost. The process, deeply integrated into the ERP system, was quickly rolled out to the individual plants. After an implementation phase of about six months, the solution was piloted at five plants in the first half of 2018. Six more plants were added three months later. The solution is now used at 16 plants in the USA, Brazil, and China. About 2,400 containers, 26,000 event messages, and 27,000 ASNs were processed by the system in the first 15 months.
The project also earned a spot in the top three at the ZF Excellence Awards 2018 in the category “Business Processes and Methods”
Success factors
Four core points were crucial to the success of the project:
- Joint project: On the part of ZF, central logistics, division logistics, IT, and the plants worked in concert with SupplyOn. This made for high acceptance and fitting accuracy of the solution.
- Commitment: The Chassis Technology Division was fully on board, enabling fast implementation and the subsequent rollout.
- Low investment: The solution required no expensive erection of infrastructures, smart tags, etc.
- Carrier independence: The solution covers all relevant sea freight carriers and is independent of direct interfaces with cargo agents.
Outlook
Other ZF plants will reap the benefits of the new solution in the future. Moreover, central logistics is planning to integrate the Material Visibility Overseas (MVO) function into SupplyOn’s standard transport management system TOMS. Right from the start, Christian Schwab, Senior Manager Corporate Freight Management, took great care to ensure that the solution could be integrated into TOMS and would be sustainable in the future, not just an isolated application.
In conjunction with the divisions, ZF plants and SupplyOn, we have implemented a smart, fast, and cost-effective solution that generates sustained positive results for our plants. We have reached a high level of transparency in our overseas transports, independent of shipper. Not to mention the rapid rollout at 16 plants around the world. In short: a complete success.
Christian Schwab
Senior Manager Corporate Materials Management, ZF Friedrichshafen AG
Benefits
- Less tracking time and effort: In the ERP system on ASN basis, material coordinators directly see which specific materials are affected by a delay. No manual information collection on external provider portals. No time-consuming search for the code numbers of a consolidated container.
- Uniform solution for all carriers and forwarders: By connecting in all relevant shipping companies, ZF can monitor its overseas transports regardless of shipper.
- Real-time information: Data are updated several times a day during overseas transport. Any changes or delays are immediately visible to the materials coordinator.
- Reduction in safety stock: The high transparency of the updated delivery status allows ZF to significantly reduce safety stocks at destination plants.
- Lower logistics costs: Early updates on delays and their effects help prevent short-term, costly special transports via air freight.
- Quick return on investment: Slim solution that is easily implemented and rolled out to plants.