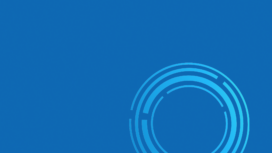
Satisfied Customers
Supply bottlenecks in aftermarket business solved by integration of 1,500 spare parts suppliers worldwide
An automotive manufacturer had to contend with supply bottlenecks in its spare parts business and the huge amount of work involved in coordination with suppliers. Unlike in production of series components, where the suppliers are integrated in an end-to-end electronic ordering and delivery process, spare parts were ordered by fax and e-mail. Numerous dispatchers had to ensure that the ordered goods were supplied on time. SupplyOn has enabled the processes in spare parts business to be controlled as efficiently as for production of series components by means of a common system. Even very small suppliers with low volumes can now be integrated in the electronic process.
Challenges
The manufacturer’s aftermarket business, which comprises not only spare parts, but also fittings and equipment for workshops and car showrooms, as well as merchandise, was controlled by means of an IT system that did not support an end-to-end ordering process. That resulted in many problems in demand planning:
- Frequent bottlenecks since it was not possible to tell whether a supplier was able to supply what was ordered and because the order process was unreliable and orders often did not arrive.
- A lot of manual work to compensate for the lack of transparency: almost 100 dispatchers were intensively involved in coordinating orders with suppliers by phone, fax and e-mail.
The process was further impeded by the fact that in aftermarket business the party who orders goods is often not the recipient – for example goods are ordered by the manufacturer in Germany, but are to be supplied to a car showroom in Asia. The lack of transparency exacerbated the problems here even further. Although the manufacturer had integrated its large suppliers in the process by EDI, most of its 1,500 aftermarket suppliers are small and medium-sized enterprises, many of whom receive orders only sporadically. Many suppliers could not even map a web-based EDI process.
The SupplyOn solution
The heart of SupplyOn’s solution is an extensive notification concept that automatically informs dispatchers when the ordering process stalls at any point, for instance when the supplier has not read the order within a defined period of time, its order confirmation has not been received or the advanced shipping notification has not been issued on time. All messages are automatically channeled into the internal SAP system.
A further part of the solution is very simple access to the electronic process, which for the first time enables even very small (and so really all) suppliers to be integrated. As part of that, SupplyOn has created a simple means of access by e-mail for the WebEDI solution used for series components: Suppliers do not have to be registered with SupplyOn. They simply receive a link via which they can access the electronic order data.
Project details
The manufacturer has been using SupplyOn in series production for a long time in order to handle ordering with suppliers in an end-to-end electronic process. That was not the case in spare parts business. The project’s objective was to harmonize the two different supply processes and handle them consistently with a central system in which all business partners are integrated.
The integration project focused on C suppliers, who are usually very small or with whom orders are placed only sporadically. Most A and B suppliers were already integrated in the electronic process by EDI or WebEDI. Rollout of the simple e-mail WebEDI process made it possible for the first time to integrate all suppliers throughout the order, confirmation, requirements reminder and financial process.
An easy upgrade allows suppliers to switch to the more convenient WebEDI integration as soon as the volume increases and they wish to benefit from the total transparency SupplyOn offers them in the order process. As part of the project, the manufacturer replaced an out-of-date internal system and rolled out a new, consolidated SAP system for requirements planning and forecasting. The SAP system performs risk analyses that use the feedback and delivery dates to calculate when a critical situation might arise. As a result of these internal risk analyses, requirements reminders are send via SupplyOn to affected suppliers. The suppliers’ feedback is also processed in the SAP system. Following internal approval, the planning data is updated.
Alongside the requirements reminder, both the manufacturer and suppliers can be notified individually of defined exceptions. As a result, the buyer only has to intervene if the supplier does not respond.
Benefits at a glance
- Complete transparency over all ordering processes thanks to integration of all 1,500 aftermarket suppliers in the electronic process, 750 of them by e-mail WebEDI.
- Reduction in the manual work and effort involved in demand planning thanks to automatic processing of the supplier feedback processes of order confirmation and advanced shipping notification (ASN) and elimination of activities such as follow-up inquiries over the phone, troubleshooting, etc.
- All messages are automatically channeled into the internal SAP system; every order transaction, including the financial processes, is fully documented in the system and can be traced.
- Savings due to minimization of out-of-stock situations thanks to notification functions at all crucial points in the process.
- Lower IT costs through use of a central system for all procurement processes in series production and aftermarket business.
You would like to get more information on Supply Chain Collaboration?
Just enter your contact details and we will get in touch with you as soon as possible.