Der automatisierte Wareneingang – Teil 1: Anlieferungen erfassen
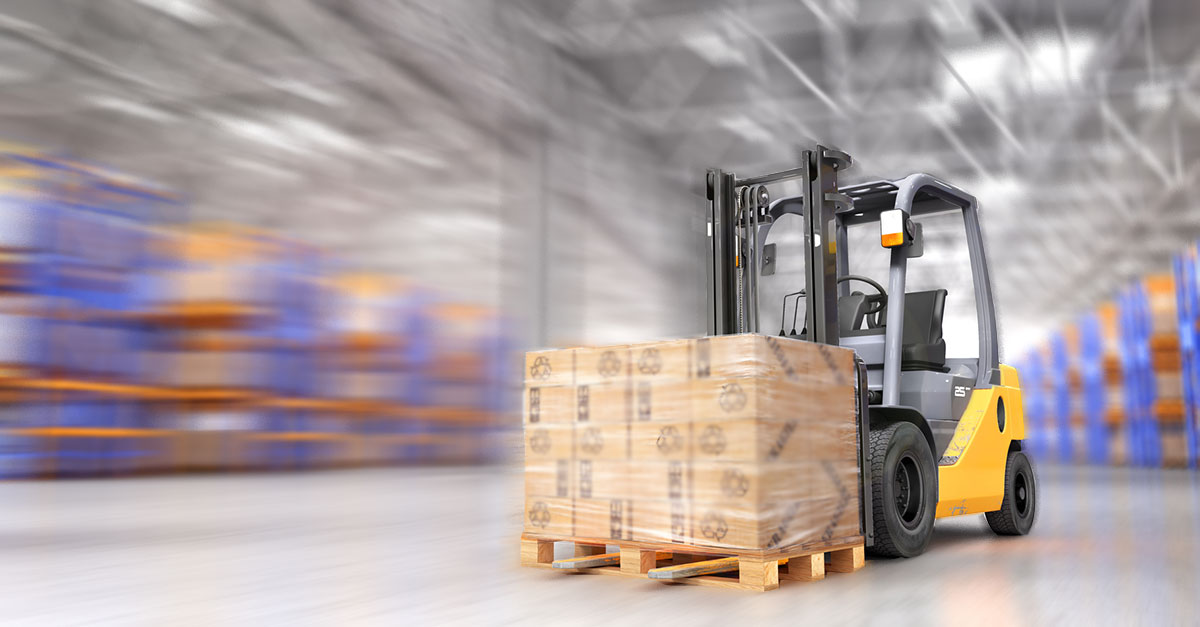
Der elektronische Bestellprozess war gerade erfolgreich eingeführt. Nach unserer Abschlussbesprechung laufe ich über das Werksgelände meines Kunden. ‚Da stehen aber viele Lastwagen vor den Toren‘, denke ich mir noch und steige in meinen Wagen.
Kaum auf der Autobahn, rufe ich gleich noch einmal meinen Kunden an: „Herr XXX, lassen Sie uns doch mal über den elektronische Lieferavisierung und automatische Warenvereinnahmung reden…“
Im nachfolgenden Gespräch stellt sich dann heraus, dass es meinem Kunden dabei wie vielen anderen fertigenden Unternehmen ergeht:
Weil keine Transparenz über den Warenzulauf herrscht, ist entweder unerwartet viel los im Wareneingang oder die Mitarbeiter haben gerade nichts zu tun. Teilweise werden die wartenden LKWs nur langsam entladen und müssen warten. Nicht selten finden sich dann Zuschläge für die Wartezeit auf der Transportkostenrechnung.
Der Lagerbestand vieler Materialien ist zu hoch, da niemand genau weiß, wann der Lieferant nun für Nachschub sorgen wird. Lieber hat man dann zu viel Sicherheitsbestand als zu wenig, was wiederum leider viel Kapital bindet.
Die Papierdokumente, die bei der Anlieferung manuell im ERP-System erfasst werden, erzeugen einen hohen Aufwand. Und das Drucken der Labels, die für die nachfolgenden Produktions- und Logistikprozesse gedruckt und auf die Verpackungen aufgebracht werden müssen, ist halt ein notwendiges Ressourcen lästiges Übel.
Haben Sie sich in einigen Punkten wiedererkannt? Dann lege ich Ihnen die Lektüre dieses Beitrags an Herz. Dieser dreht sich um genau diese Herausforderungen und soll Ihnen folgende Fragen beantworten:
- Wie plane ich meine Ressourcen im Wareneingang ideal?
- Wie vermeide ich langwierige und kostenintensive Standzeit der Spediteure?
- Wie kann ich das in Sicherheitsbeständen gebundene Kapital reduzieren?
- Und wie eliminiere und reduziere ich die manuellen und fehleranfälligen Wareneingangsprozesse?
- Wie schaffe ich es, kostenintensives Relabeling zu vermeiden?
Die Antwort auf diese Fragen liefere ich Ihnen schon vorab: Indem Sie Ihren Wareneingang auf automatisierte und elektronische Prozesse umstellen!
Wie dies funktioniert und was Sie dabei beachten sollten, möchte ich Ihnen gerne im Folgenden aus der Praxis heraus erläutern.
Elektronische Lieferavisierung als Grundlage (ASN-Prozess)
Ein essenzieller Baustein ist dabei die elektronische Avisierung der Waren durch den Lieferanten, welche im Normalfall per sogenannter „ASN“ (Advance Shipping Notice) erfolgt. Der Lieferant erfasst vorab einige Grunddaten, die dann bereits bei Abfahrt des Spediteurs elektronisch übermittelt werden und die Grundlage für den effizienten Wareneingang bilden.
Wichtige Informationen hierbei sind zum Beispiel:
- Lieferscheindaten des Lieferanten wie z.B. Nummer des Lieferscheins und der Lieferposition
- Geplantes Anlieferdatum (wird ggf. aufgrund hinterlegter Vorlaufzeiten automatisch errechnet)
- Materialdaten wie z.B. Materialnummer, Name und Menge, ggf. Charge und Herkunftsland
- Bestellnummern oder Rahmenvertragsnummern
- Verpackungsinformationen zu den Transportbehältern oder Paletten
Die Erfassung dieser Daten kann entweder im ERP-System des Lieferanten erfolgen, oder in einer Web-Plattform. Nutzt der Lieferant sein eigenes ERP, müssen die Daten per EDI-Schnittstelle an das Kundensystem übertragen werden. Dies setzt allerdings voraus, dass der Kunde mit all seinen Lieferanten eine solche EDI-Verbindung eingerichtet hat. Erfahrungsgemäß ist das selten der Fall. Meist kann zwar ein großer Teil des Beleg- und Bestellvolumens per EDI ausgetauscht werden. Eine vollumfängliche Lösung bleibt dann aber meist eine schöne Vision.
Mit Hilfe einer webbasierten Kommunikationsplattform, wie zum Beispiel der SupplyOn Purchase-to-Pay-Lösung, können sowohl Lieferanten mit EDI-Schnittstelle als auch kleine, technisch weniger reife Lieferanten eingebunden werden. Das dürfte zu einer nahezu 100%igen Abdeckung des Prozesses führen.
Durch die Nutzung einer solchen Plattform lassen sich dann zusätzlich ausgeklügelte Reports zur Lieferqualität der Lieferanten erzeugen. Im Falle von Abweichungen kommt ein umfassendes Alerting-System zum Einsatz. Es informiert sowohl den Lieferanten als auch kundenseitig den Materialplaner automatisch, beispielsweise über überfällige Lieferungen. Ein zeitaufwändiges, manuelles und dauerhaftes Überwachen der Supply Chain ist damit überflüssig. Der entsprechende Mitarbeiter muss nur im Falle einer Abweichung eingreifen.
Verbesserte Kapazitätsplanung durch höhere Transparenz
Aber zurück zum Avisierungsprozess. Die Informationen, die der Lieferant im Lieferavis erfasst hat, werden nun strukturiert in Ihrem ERP-System abgelegt. Dort wird daraus eine so genannte Anlieferung erzeugt. Auf Basis dieser Daten haben Sie also bereits einige Tage oder sogar Wochen vorab die Information, welche Waren sich im Zulauf befinden und können eine deutliche genauere Kapazitätsplanung im Wareneingang erstellen.
Sie wissen nun ebenfalls, dass ein Material, das eventuell einen Engpass erzeugen könnte, sich im Zulauf befindet. Diese Informationen können Ihre Mitarbeiter in die Material- und Produktionsplanung einbinden. Damit können Sie systematisch kapitalintensive Sicherheitsbestände reduzieren. Zudem sinkt der Planungsaufwand bei Ihren Mitarbeitern erheblich, weil viele manuelle Nachfragen und Abstimmungen mit den Lieferanten überflüssig werden.
Weil die Kapazitäten im Wareneingang deutlich näher an den tatsächlichen Bedarf angepasst sind, reduzieren sich Wartezeiten für die Entladung von ankommenden LKWs. Ihre Mitarbeiter in der Anlieferung sind somit hinsichtlich Mehrarbeit und Leerläufe ideal ausgelastet.
Reduktion von manuellen Aufwänden im Wareneingang
Der wahrscheinlich größte Gewinn, den Sie aus einem automatischen Wareneingang ziehen können, ist dabei aber die Reduzierung manueller Tätigkeiten. Müssen heute alle Lieferungen in einem manuellen, fehleranfälligen Prozess vom Papierlieferschein in das System übertragen werden, sind im Falle einer elektronischen Anmeldung der Waren bereits alle relevanten Daten vorhanden. Um die Güter zu vereinnahmen, muss der Mitarbeiter nur per Referenz (also Bestellnummer, Lieferantennummer, Lieferscheinnummer) den entsprechenden Datensatz im System identifizieren und kann diesen dann per Knopfdruck einbuchen. Alle relevanten Informationen sind ja bereits in Ihrem Systemen vorhanden.
„Piep“ und weg – die automatische Vereinnahmung per Scanner
Während des Avisierungsprozesses hat der Lieferant bereits Dokumente, wie den Lieferschein oder Transportauftrag, gedruckt. Diese sind den Waren beigelegt. Warenbegleitlabels werden auf den Packstücken und Handling Units – etwa Palette oder Gitterbox – angebracht. Dabei können die Labels verschiedenste Informationen zum Material oder zum Lieferanten enthalten. Wichtige Informationen sind hier meistens maschinenlesbar in Form eines (2D-) Barcodes angedruckt.
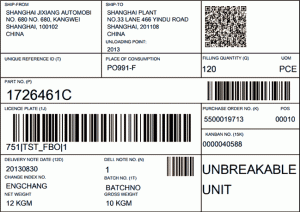
Es gibt einige Standardlabels, wie zum Beispiel VDA 4902 (besonders in der europäischen Fertigungsindustrie verbreitet), ODETTE oder das relativ moderne GTL-V3-Label, das sich mehr und mehr als weltweiter Standard durchsetzt.
Manchmal entsprechen die Standardlabels jedoch nicht den Vorgaben des Kunden. Zum Beispiel, weil sie aufgrund ihrer Größe nicht für Kleinladungsträger geeignet oder die Informationen auf den Labels nicht ausreichend sind. Dann kann ein kundenspezifisches Label zum Einsatz kommen.
Hierbei ist allerdings zu beachten, dass der Lieferant ebenfalls in die Lage versetzt werden muss eben dieses Label zu drucken. Bei Standardlabels dürfte dies meist der Fall sein. Die Programmierung eines kundenspezifischen Labels stellt die meisten Lieferanten jedoch vor technische und prozessuale Probleme. Hier kann die Nutzung einer Standardplattform wie SupplyOn, welche automatisiert alle relevanten Dokumente für den Lieferanten bereitstellt, eine große Unterstützung sein.
Statten Sie Ihren Wareneingang nun noch mit einem Scanner aus, können ankommende Lieferungen vollautomatisch per Scan identifiziert und vereinnahmt werden. Das reduziert den Aufwand noch einmal deutlich. Die automatische Vereinnahmung ist übrigens auch mit Szenarien wie RFID-Tags oder Bluetooth-Sendern kombinierbar, die dann anstatt des Scannen des Labels für die Identifikation des Datensatzes sorgen.
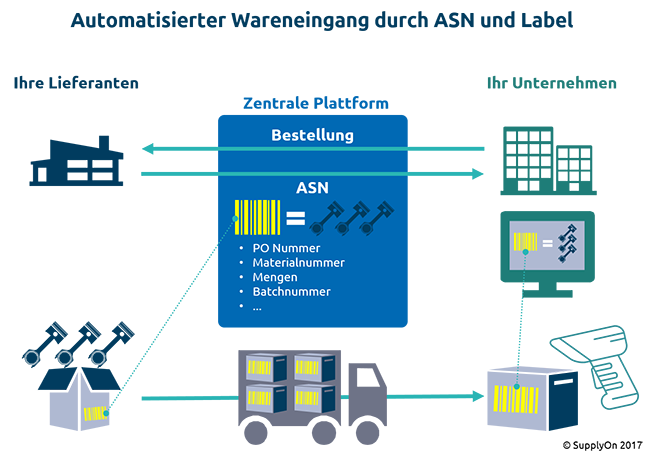
Bei meinem Kunden hat das wunderbar funktioniert – die Scanner verrichten fleißig piepend Ihren Dienst und die prozessualen Aufwände sind deutlich zurückgegangen. Wie wir dann noch den zeitaufwändigen Prozess des Relabelings abgeschafft haben, lesen Sie im Teil 2 meines Beitrags.
Ich hoffe, ich konnte Ihnen bis hierhin schon den einen oder anderen Denkanstoß geben und freue mich auf Ihre Kommentare zu Ihren Erfahrungen und Herausforderungen!
Ihr Florian Böhm