Hirschvogel automates its consignment warehouse using SupplyOn
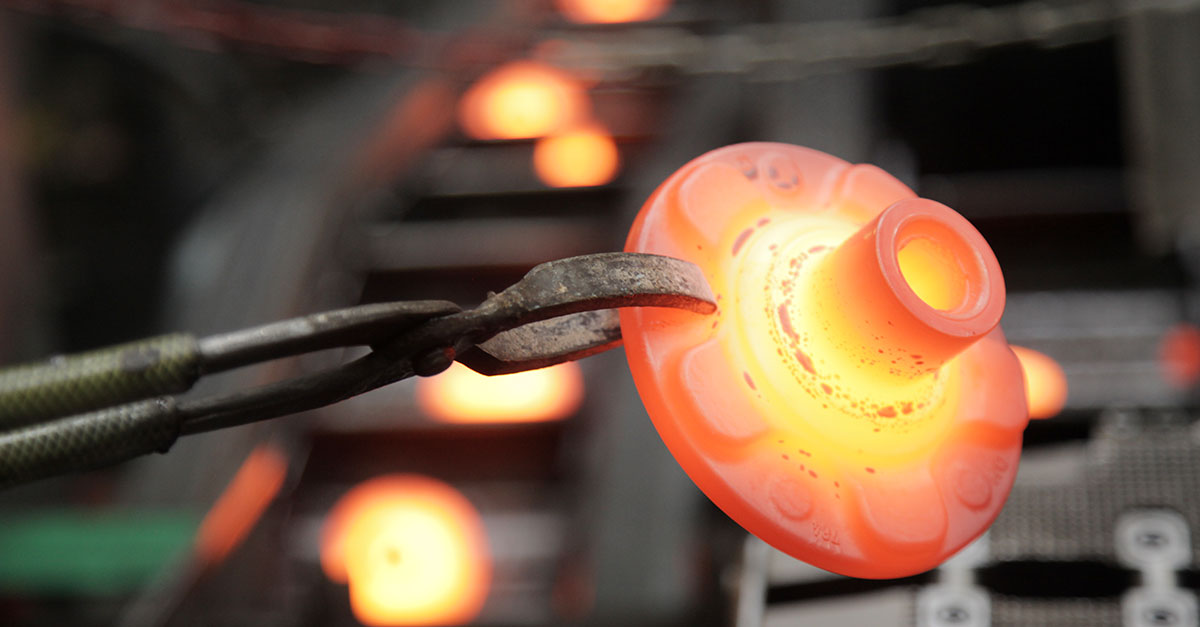
Consignment warehouses have become trendsetters. But managing them is an extremely complex task and, as volumes rise, economically not viable anymore without digitalized processes. Taking this into account, automotive supplier Hirschvogel recognized the need to automate the processes used for its customer Schaeffler – with the help of SupplyOn.
Rising demands call for the automation of consignment warehouses
The job of managing consignment warehouses has become much more challenging in recent years. The reason for this change is quite simple: Customers want to have a bigger and bigger supply cushion on site – that is, increasing numbers of components must be kept on hand as material so that the customers can access them faster. Such needs require suppliers to undertake an Olympian production and logistical effort to ensure that the customer always has a sufficient amount of products on site.
As a result of rising volumes, this job simply cannot be done manually any longer. The job of recording goods received and issued is very time-consuming and error-prone in and of itself. Regular stock comparisons conducted by telephone, fax or e-mail are virtually impossible: Either there is not enough stock information on hand or significant differences exist in the information held by the supplier and the customer.
The result: costly special deliveries resulting from an unexpectedly empty warehouse, are almost inevitable. The same is true for high depreciations on the annual stock inventory. Other problems arise when old stocks are not removed in accordance with the “first in & first out” principle or leftover containers remain in storage.
For this reason, Hirschvogel Holding GmbH began to digitalize and automate this process at its business locations in Germany at an early stage. When Schaeffler wanted to expand its partnership with the forging specialists as part of their auxiliary production activities in Eisenach, Hirschvogel realized from the outset that the consignment warehouse there would have to be automated.
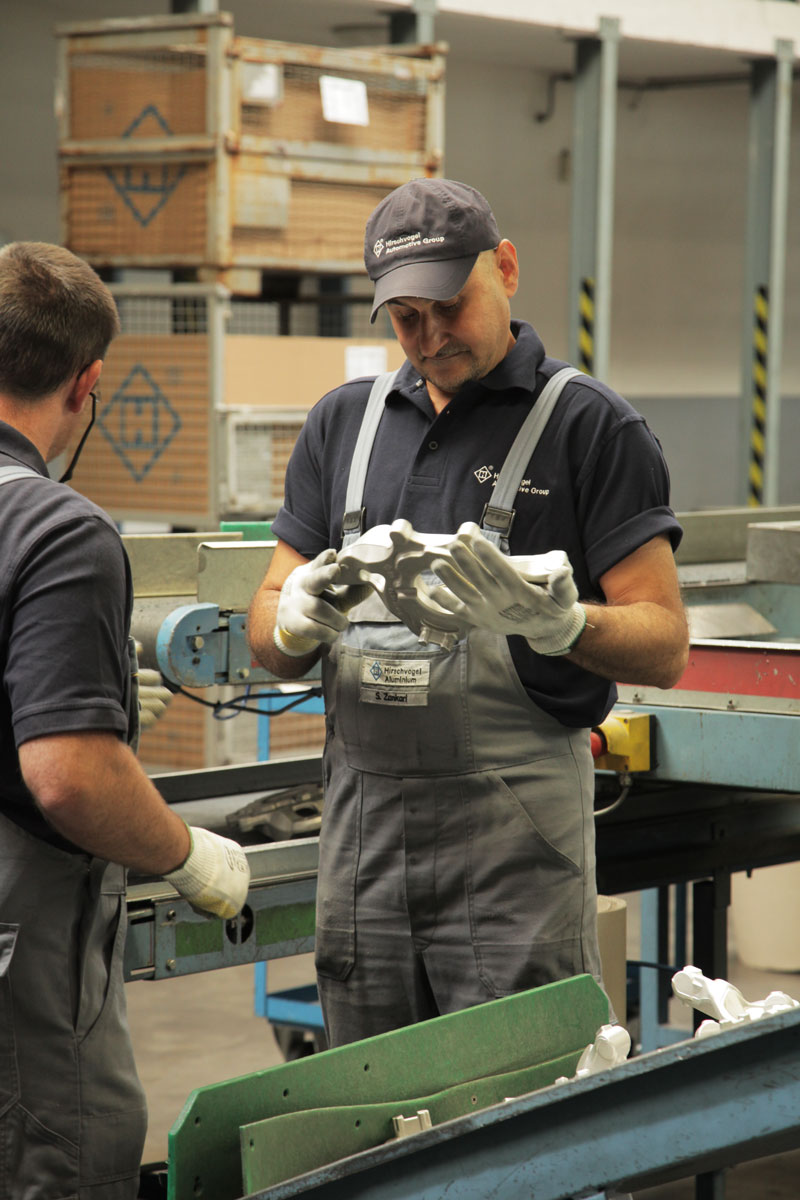
The introduction of SupplyOn
The initial preparations began in 2015 after a kick-off. For this purpose, Schaeffler brought its preferred solution partner, SupplyOn, on board. SupplyOn was no stranger to Hirschvogel. From 2001 on, the automotive supplier has been using an array of solutions with its customers on the SupplyOn platform.
To create a fully automated consignment warehouse, removals and comparisons should be seamlessly displayed in Hirschvogel’s ERP system via an EDI link. SupplyOn uses the latest EDIFACT standard as the data format. An intensive test and development phase followed in order to ensure all data are correctly processed by the in-house format used at Hirschvogel.
The expertise of SupplyOn played a key role here, said Matthias Zimmermann, who oversaw the IT aspect of the project for Hirschvogel in the area of Business Partners & Services: “One major benefit for us was that SupplyOn is a specialized service provider with whom we could conduct detailed discussions about our technical needs.” As a result, the format for loading, batch numbers, etc. could be easily changed. Because Hirschvogel uses stocks that are managed in batches, it placed a high priority on ensuring that this information could be displayed and automatically processed.
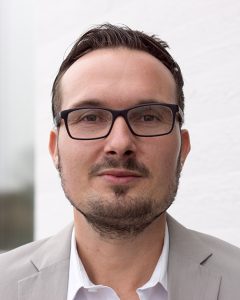
“With SupplyOn, we had a specialized service provider on board with whom we could conduct detailed discussions about our technical needs. This simplified the implementation process considerably.”
Matthias Zimmermann, Business Partner & Services, Hirschvogel Holding GmbH
The intensive groundwork paid off: As a result, it was possible in February 2016 to make the switch from the test system to the productive system over night and to immediately update all incoming data correctly.
The department has enjoyed a massive reduction in its daily operations ever since. Demands on personnel have fallen significantly as well – from several hours per week to a few minutes per day. Above all, issuing invoices and handling returns has become much easier: In the past, issue postings were made only once a week, a practice that was a continuous source of problems at the turn of the month. After all, the calculated alloy and scrap surcharges change each month – and the basis for invoice processing with them.
This is no longer a problem as stock and issue postings are now prepared on a daily basis. Returns are also announced at an early stage, a step that ensures they can be easily processed.
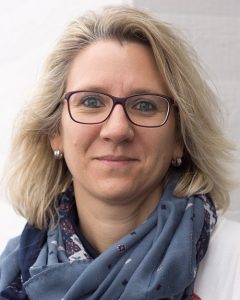
“Thanks to real-time accounting, we have a high level of transparency on stocks. From shipment planning to returns processing and invoicing – our work has improved tremendously. Above all, we can now employ our resources much more productively.”
Michaela Warth, Specialist Consignment Warehouse, Hirschvogel Holding GmbH
Benefits for Hirschvogel
- Total transparency about stocks and issues
- Sustantial time savings produced by a completely automated process that extends from stock issue to credit note
- Real-time invoice preparation and thus the correct invoicing of surcharges
- Simplified returns processing, shipment planning and stocktaking
- Significantly fewer coordination and clarification requirements with customers and forwarding companies
- Seamless communication without any manual intervention or errors and with fewer human resources
- Personnel flexibility because training periods are much shorter
About Hirschvogel
Hirschvogel Holding GmbH, based in the Bavarian town of Denklingen, is one of the largest global automotive suppliers in the area of steel and aluminum forging and their subsequent processing. Its customers include all renowned automobile manufacturers and suppliers around the world. With locations in China, India, Mexico, Poland and the United States, the family-run company generated consolidated sales of €931 million in 2015 and employs about 4,500 people.