How to best manage geo-related risks in your supply chain
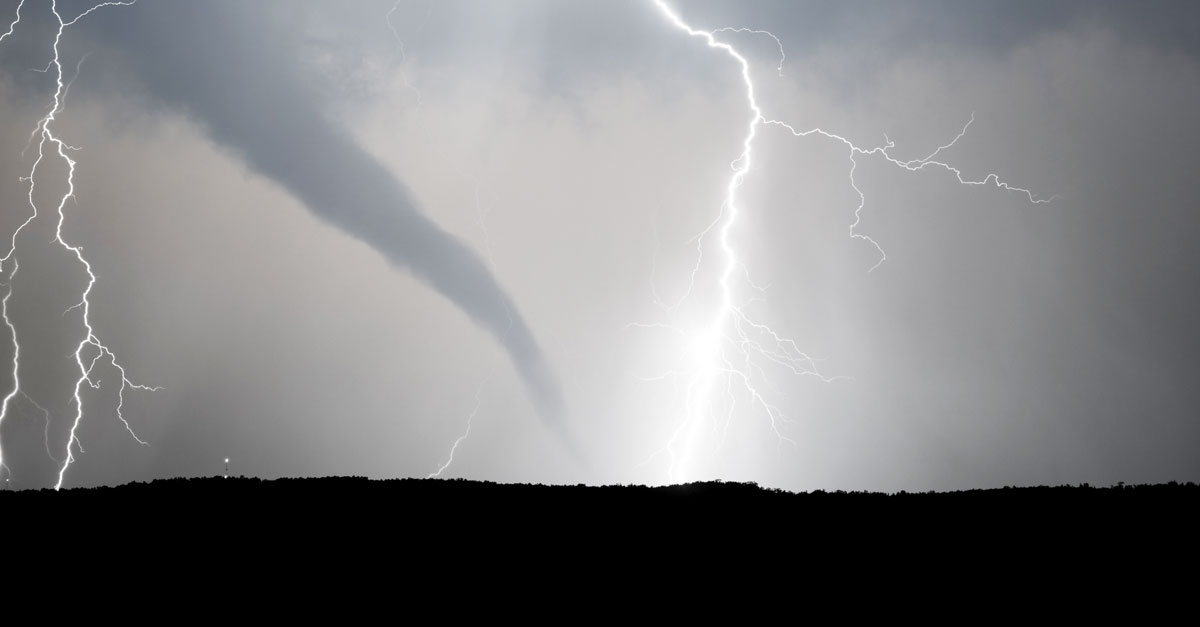
The past two years have been marked by unprecedented supply chain disruptions. It’s not just the transport routes, but also the production of goods itself that is severely impacted: New local or regional Covid lockdowns keep slowing down manufacturing, especially in Asia. The ongoing chip shortage hits more and more industries. The power outage in Texas first knocked out the local petrochemical plants in February — then, its effects swept across the entire plastics supply chain worldwide. … The list could go on and on.
And then climate change. It is causing ever more frequent and ever more severe natural hazards. The floods on the River Ahr in Germany in mid-July, for instance, completely demolished the region’s infrastructure as well as numerous plants. Some impacted businesses still operate with substantially reduced production capacities, even almost half a year later.
The overall problem: raging hurricanes, floods and fires are no longer limited to the “classic” regions. At the same time, damage severity keeps increasing.
So, the question of all questions for supply chain managers is: Which risks are lurking in my supply chain and where? Which plants and suppliers are particularly at risk, today and in the future?
Detailed geo-risk assessment, tailored to your needs
To answer these questions, SupplyOn’s Strategic Risk Management draws on risk data from reinsurers such as Munich Re or Swiss Re. It analyzes the geo-specific risks for each supplier plant in a wide range of categories, from earthquakes and volcanic eruptions to hurricanes, tornadoes and hailstorms to floods and storm surges.
The assessment and rating of these risks can be adapted individually to each supply chain. Thus, on a ten-point risk scale, a location may enter the red zone at a “9” for hail or lightning, while the traffic light for earthquakes or floods may already turn yellow at a “3”.
But it is not only the threshold values for the individual risk levels (or “scores”) that can be customized. The scope of the scale, the number of hazard levels and their respective color display are also adaptable to a user’s needs. Thus, a six-level scale with four different shades of blue is just as feasible as a three-color traffic light coding (green, yellow, red) on a scale of ten.
But that’s not all: companies can integrate risk information from other sources or even add their very own risk categories. More on that in a moment.
In the end, all risk scores are aggregated into an overall score. Based on the “worst color wins” logic, it then displays the least favorable score point. As such, supply chain managers can now immediately identify critical supplier plants with simply a glance at the map.
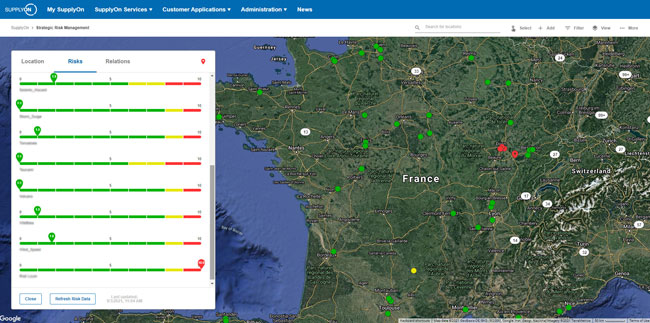
Specific geo risks, short and long-term
In addition to natural disasters, however, there are other location-related risk sources for the supply chain. Take a supplier, for example, who operates a production facility in a metropolitan area with an extremely high congestion potential. This may have a lasting negative impact on his on-time delivery (OTD) performance. This, in turn, quickly jeopardizes any sophisticated just-in-time (JIS/JIT) production.
Also, sustainability and compliance issues may play a role in site-based risk assessment. For instance, plants operating in regions that are deemed critical with regard to a company’s ESG guidelines or legislations, such as the German Supply Chain Ac, might get negative risk scores.
And last but not least, particularly the last year and a half have proven that more or less short-term regional events can also cause enormous, long-term disruptions to supply chains.
To quickly identify such risks, SupplyOn’s Strategic Risk Management lets you flexibly define your own risk categories. Supply chain managers simply draw circles or polygons over the affected regions on the maps. Whether it’s the Frankfurt area, with its high levels of congestion, or the Wuhan region, which was completely closed off for three months at the start of the coronavirus pandemic, or southern US, which was hamstrung by exceptional winter conditions and resulting power outages, or political conflicts such as the current one on the border between Poland and Belarus. Whatever the cause, companies immediately see its direct effects. They know right away, whether any of their supplier plants are affected and, if so, to what extent.
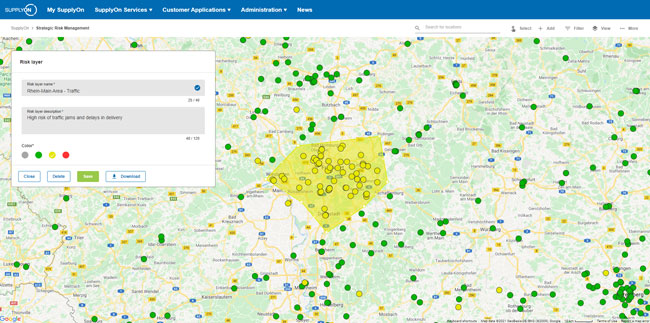
Threats to the flow of materials, clearly and precisely
Yet, supply chain managers not only see which suppliers or which supplier plants are at risk. By linking the location and the material produced there, risk assessment can be determined at item level. Thus, supply chain managers can precisely assess how the identified risks would affect their own production if the worst came to the worst.
By the same token, the solution also enables filtering by specific materials and hence detecting the location risks of the corresponding supplier plants. This allows for a thorough assessment of material-related supply chain risks on a more global level.
Forewarned is forearmed(?)
This immediately raises the question: Now, how can companies minimize the identified supply risks? After all, a supplier cannot simply relocate its production facility to another site overnight. And terminating a long-standing, close and trusting supplier relationship only because of the identified risks might also not be the best advice.
Negotiate safeguards
Companies can, however, agree on specific hedging measures with their suppliers, such as the erection of protective walls and flood barriers in case of flooding risks. Another option would be to define business continuity measures (BCM) together, for example the outsourcing of production capacities to other plants, at an early stage in order to prevent a disruption in the supply chain.
Integrate geo-risk information in supplier selection and evaluation
On top, risk information is extremely valuable for supplier selection and evaluation in the event of awarding new contracts, too. If multiple suppliers’ bids barely differ in terms of price and quality, risk assessment can tip the scales. Most importantly, though, companies already know before they sign the contract what potential risks to their own production their decision may entail.
Of course, this very same information can also be used the other way around when companies come to make decisions about where to locate production facilities themselves.
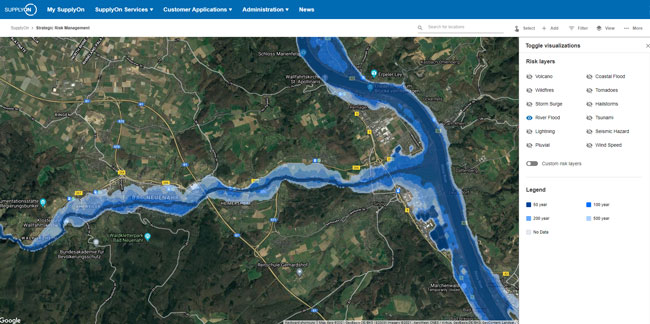
Fit for future
The current supply chain woes are likely to stay with us for a while. Geo-strategic risks, however, will continue to increase, as a result of climate change. By all accounts, they will become more frequent, more severe and hit more and more regions. It is all the more important, therefore, to be aware of the risks to your own supply chain.
This is precisely where the SupplyOn Strategic Risk Management provides valuable assistance. In the event of sudden local or regional events, the solution facilitates incident risk management, making the potential impact on the flow of materials immediately transparent. When it comes to medium- to long-term risk strategy, companies can use the existing risk information to even better mitigate supply chain risks.
All of this adds up to making the supply chain more resilient, ready for the (geo- and climate-related) challenges of the future.