Swap container and load carriers without conflicts – Simply create transparency to reduce costs
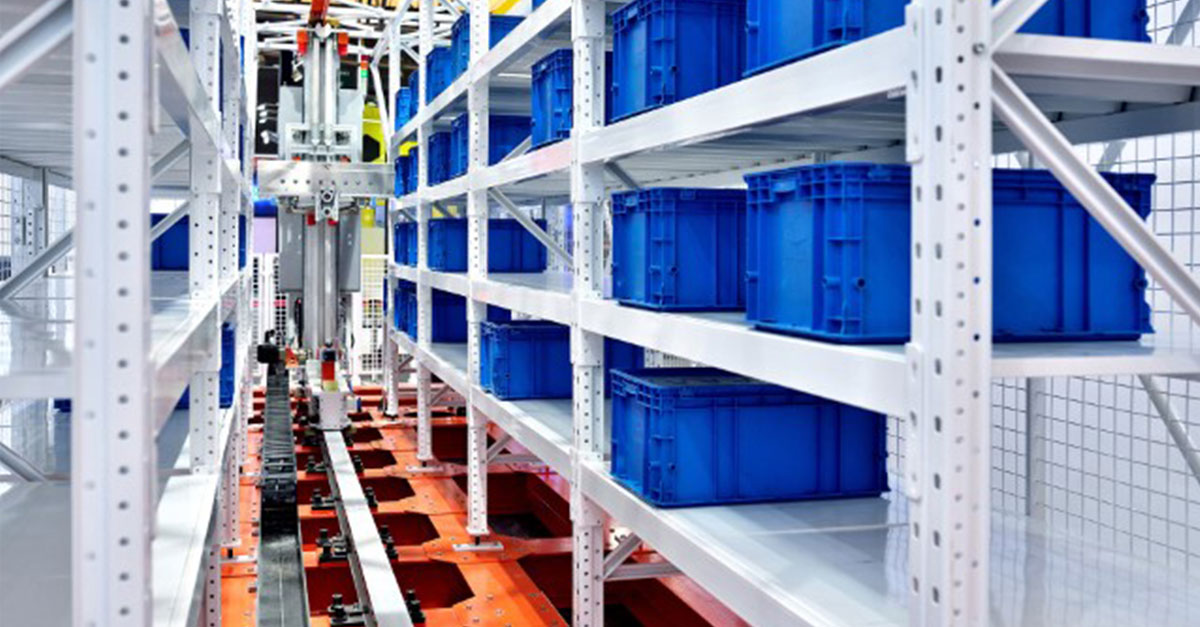
Disappearing containers, isolated systems and inventories, unnecessary transport costs due to empty rides, chaos in billing container rentals. These are just a few of the challenges faced by the manufacturing industry in the daily management of containers and load carriers.
Small as well as large load containers, pallets, wire mesh boxes, and especially special load containers represent a considerable cost factor. If they are lost and new ones have to be purchased, container costs quickly skyrocket. Digital control of load containers by means of an empties management software creates transparency in the container cycle. The type and number of containers, their current whereabouts, and their respective retention periods are thus visible to all exchange partners in real time. The use of load carriers is organized much more effectively and the effort for used load carriers and their management is drastically reduced. In most cases, the inventory at the start of the jointly used container management system already reveals enormous values of previously “invisible” stocks.
Save time through automated container bookings
The networking of all partners involved in the container cycle breaks down the individual data silos and enables a cross-company data pool. Combined with real-time data exchange, this is the ideal basis for automated recording of container inflows and outflows through intelligent, rule-based mechanisms. Whether ordering empties, scheduling, inventory reconciliation, or billing, these processes are automated thanks to a common data pool and on the basis of delivery data. This eliminates the need for cost-intensive and error-prone manual entries or re-keying. This leaves more time for more demanding tasks.
Coordinated full and empty container transports
With the common data pool, the cycle of full and empty containers and their transports can be efficiently organized. For example, the system can automatically calculate the latest empties order date for the supplier from delivery call-offs – as in the automotive industry. The simultaneous picking up of empty and loaded containers when goods or materials are delivered can also be efficiently planned. As a result, transports are condensed, empty runs are reduced to a minimum and the CO2 balance is improved.
Transparent billing spurs cooperation
The billing of container rentals, transport costs, or additional costs due to replacement containers often leads to tensions between the partners in the container exchange. However, if all partners can see when, where, and for how long which containers have been used, billing becomes transparent and the potential for conflict is reduced. In addition, the system uses rule-based intelligence to detect discrepancies, for example, in the quantities ordered and delivered. Should this be the case, the system automatically makes suggestions for complaints and thus also simplifies the day-to-day procedures in billing and controlling. Discrepancies can be clarified immediately and do not come up for discussion months later.
Conclusion: Containers can be managed extremely economically
EURO-LOG’s empties management system makes exchanging load containers a real pleasure – transparent and extremely economical. The system links all logistics partners and digitally maps the container cycle. The movements of all containers and transport aids between plants, suppliers, transport and logistics service providers become traceable. The result: consistently transparent container flows in real time, hardly any more hassle and a fast payback of the system.
Want to learn more about our container management system? Let’s connect – we look forward to hearing from you at anfrage@eurolog.com