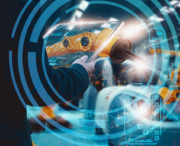
Parts Traceability
Holistic approach to simplify traceability and improve product quality
Traceability:
An essential asset for volatile supply chains
Products must be traceable down to the raw material level in order to quickly resolve quality issues and continuously improve product quality. If seamless traceability is ensured, the costs of recalls can be minimized, fake products can be tackled, production processes for quality control can be monitored and quality assurance processes can be optimized.
In order to achieve this, SupplyOn’s Parts Traceability solution makes use of what is known as a digital twin. This involves collecting all the data generated during the production of a specific product and storing it as a digital copy. The digital twin created that way provides valuable information for continuous quality improvement already during production. Once the end product has been delivered, it can be used to quickly trace which parts and batches are affected in the event of a recall.
One solution – two use cases
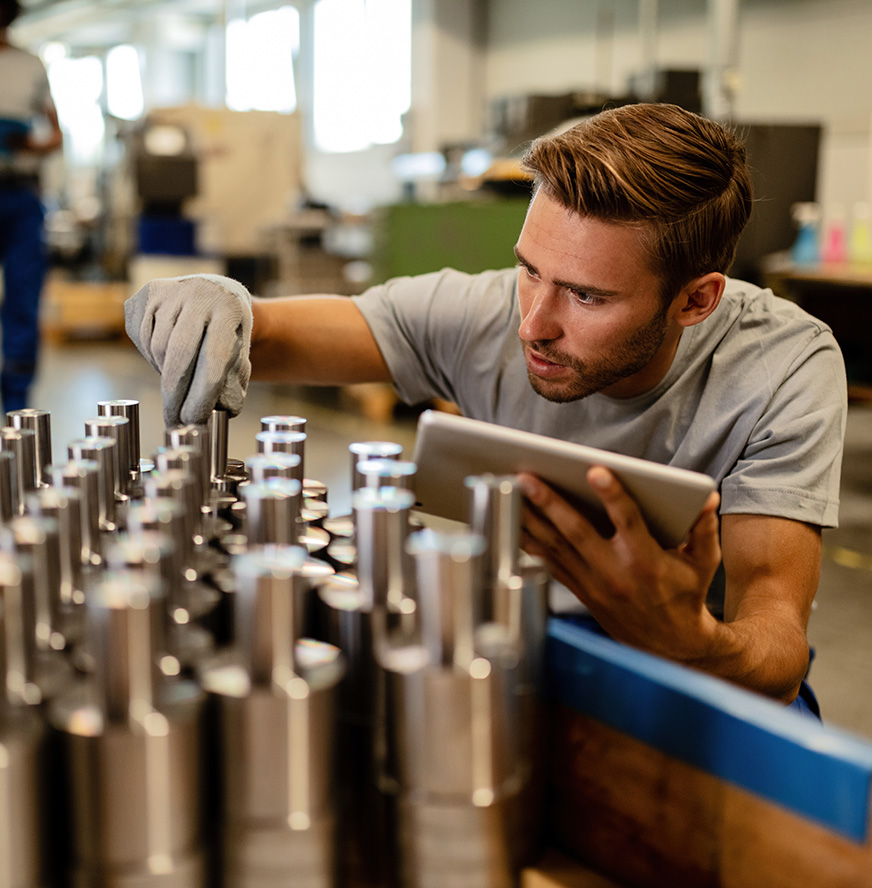
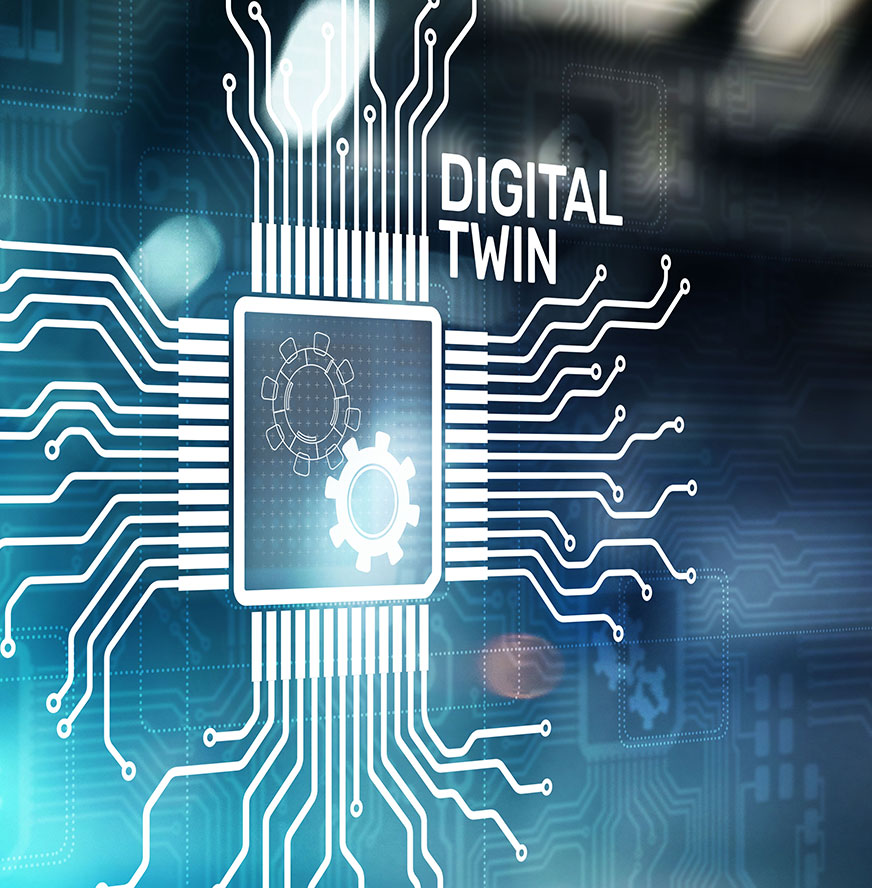
Quality assurance
In this use case, you share your quality check plans for specific components with your supplier via SupplyOn: How to measure? At what frequency? With which tolerance? The testing plans are exchanged directly from your internal quality systems via an API interface. The plans are available to the supplier via the SupplyOn web interface, where the test results are entered. The test report is automatically transferred to the internal systems via the interface. If tolerances are exceeded, alerts inform both sides immediately. If quality is gradually deteriorating, the system predicts when the tolerance limit is likely to be exceeded. A connection via API interface is also possible on the supplier side.
Digital twin
In this use case, a digital twin is created on the basis of all data generated for a specific part. This ranges from serial and batch numbers to data from check reports as well as order and transport data from ERP systems. From this data, complex component trees are created. In the event of a recall, this information is of immense value: Using the component tree, it is possible to quickly identify which specific parts are installed in which end products and need to be replaced.
Your benefits of
Parts Traceability
Smart, integrated functionalities at a glance:
- Detailed search and filtering functions
- Up- and download functionality
- Integration possibility for different systems on both sides via API interfaces that are easy to set up
- Creation of configurable batch and serial labels with QR code
- Transparent document storage
Do you want to make your parts traceable now?
Just enter your contact details and we will get in touch with you as soon as possible.